Understanding Lean Thinking: 5 Key Principles Explained and Applied
In today's competitive landscape, businesses are constantly seeking ways to improve efficiency, reduce waste, and enhance productivity. One methodology that has gained widespread recognition for achieving these goals is Lean Thinking. Rooted in a philosophy of continuous improvement, Lean Thinking encompasses five fundamental principles: Value, Value Stream, Flow, Pull, and Perfection. Let's delve into each principle and explore how they can be practically applied across diverse industries.
Principle 1: Value
At the core of Lean Thinking lies the concept of 'Value.' Value is defined as anything that the customer is willing to pay for. It’s crucial to identify and understand the specific needs and desires of the customer to deliver products or services that add value. For instance, in manufacturing, value could be a product feature that directly benefits the end-user, while in a service industry, it might be delivering solutions that fulfill customer needs promptly and efficiently.
Application: Start by understanding customer needs and preferences through surveys, feedback, and data analysis. Then, align processes and resources to focus on delivering value by eliminating non-value-added activities, thus reducing waste.
Principle 2: Value Stream
The 'Value Stream' refers to the end-to-end sequence of activities and processes required to deliver a product or service, from raw materials to the customer's hands. Understanding and mapping the Value Stream helps identify each step's contribution to value addition and waste.
Application: Conduct Value Stream Mapping (VSM) to visualize and analyze the entire workflow. Identify bottlenecks, unnecessary steps, and areas of waste within the Value Stream. This allows for streamlining processes and optimizing efficiency across industries, from manufacturing to healthcare and software development.
Principle 3: Flow
'Flow' refers to the uninterrupted movement of products, services, or information through the Value Stream. The objective is to eliminate interruptions, delays, or disruptions that hinder the smooth flow of work.
Application: Implement strategies to ensure a continuous flow of work. For instance, in manufacturing, Just-in-Time (JIT) production minimizes inventory and ensures products move through the production line smoothly. In healthcare, optimizing patient flow through hospitals reduces waiting times and improves overall service delivery.
Principle 4: Pull
'Pull' involves producing goods or delivering services based on actual customer demand rather than pushing excessive inventory or output into the market. This principle emphasizes creating a demand-driven workflow to minimize waste.
Application: Adopt a pull-based system where production or service delivery responds directly to customer demand. For example, retailers use demand-driven inventory management to restock items only when there's a customer order, reducing excess inventory and associated costs.
Principle 5: Perfection
The pursuit of 'Perfection' is an ongoing journey of continuous improvement. It involves constantly striving for excellence by eliminating waste, optimizing processes, and fostering a culture of continuous learning and innovation.
Application: Encourage employees at all levels to participate in identifying opportunities for improvement. Implement a culture that embraces change and encourages experimentation. Regularly review processes and seek ways to further enhance efficiency and quality.
Practical Application Across Industries
The principles of Lean Thinking are highly adaptable and applicable across various industries:
- Manufacturing: In manufacturing, Lean Thinking is traditionally associated with reducing waste in production processes, improving product quality, and shortening lead times.
- Healthcare: Lean principles have been effectively applied in healthcare to streamline patient flows, optimize hospital operations, and reduce wait times for appointments or treatments.
- Software Development: Agile methodologies in software development, emphasizing iterative development and customer collaboration, align with Lean principles of delivering value and continuous improvement.
- Service Industry: Lean Thinking is increasingly being used in service industries like banking, hospitality, and logistics to improve customer experiences by reducing wait times, errors, and unnecessary processes.
Conclusion
The principles of Lean Thinking—Value, Value Stream, Flow, Pull, and Perfection—form the foundation for continuous improvement across industries. By understanding and applying these principles, organizations can optimize processes, eliminate waste, and deliver value to customers more effectively. Embracing Lean Thinking not only drives efficiency but also fosters a culture of continuous improvement, positioning businesses for sustained success in today's dynamic market.
Understanding Lean Thinking: 5 Key Principles Explained and Applied
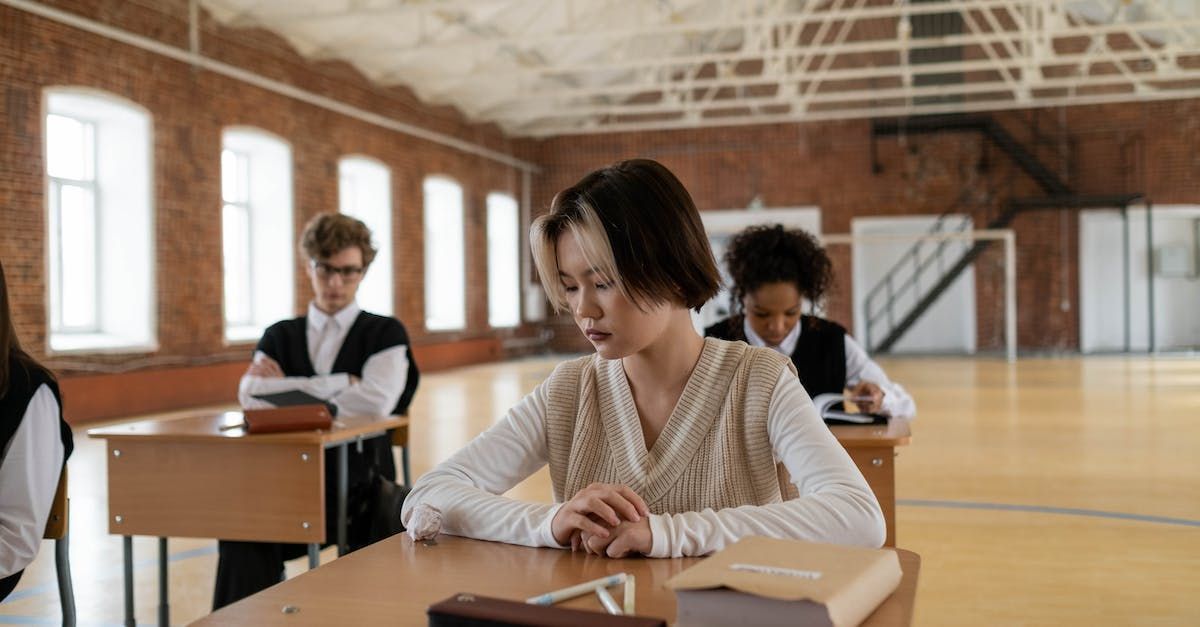
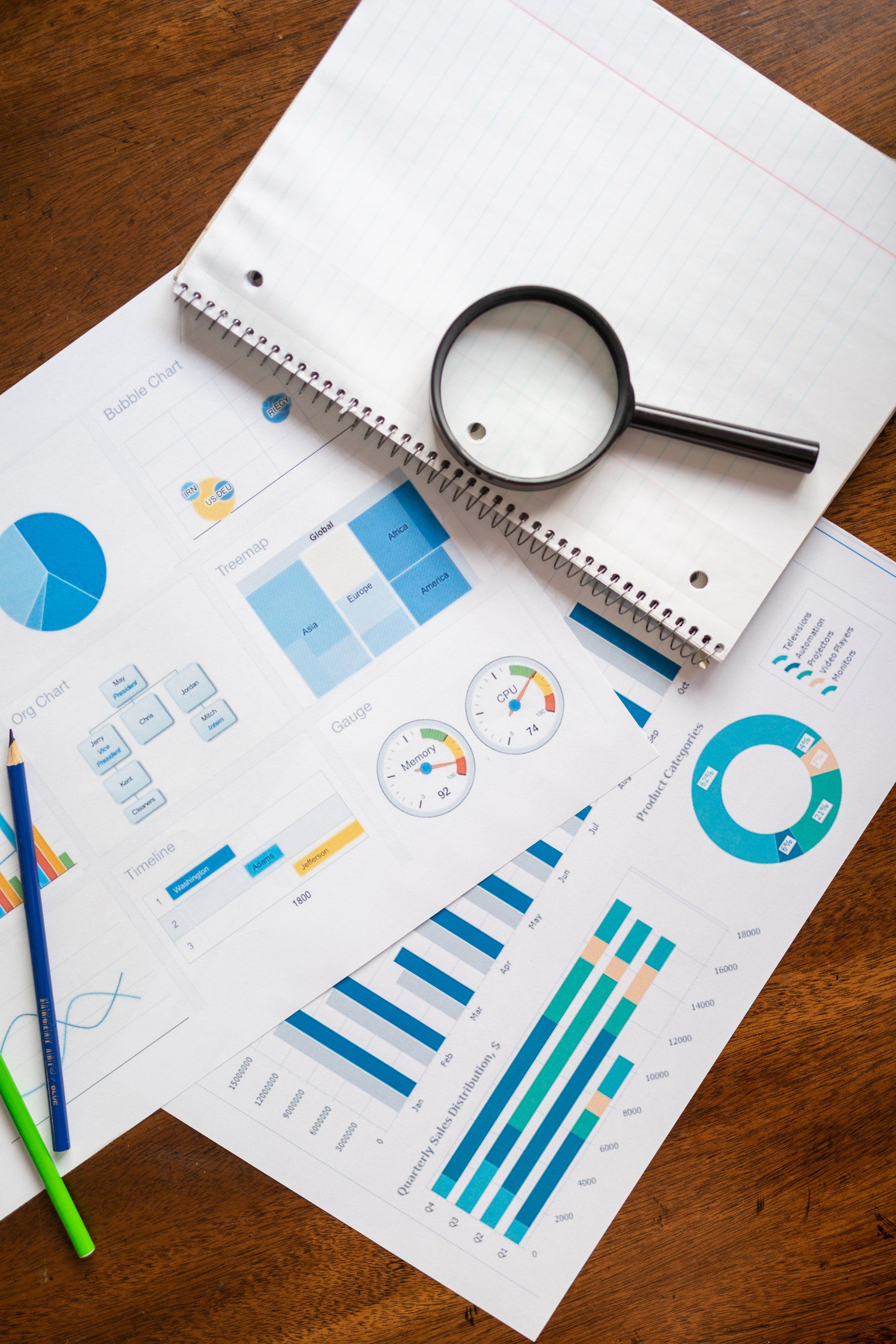
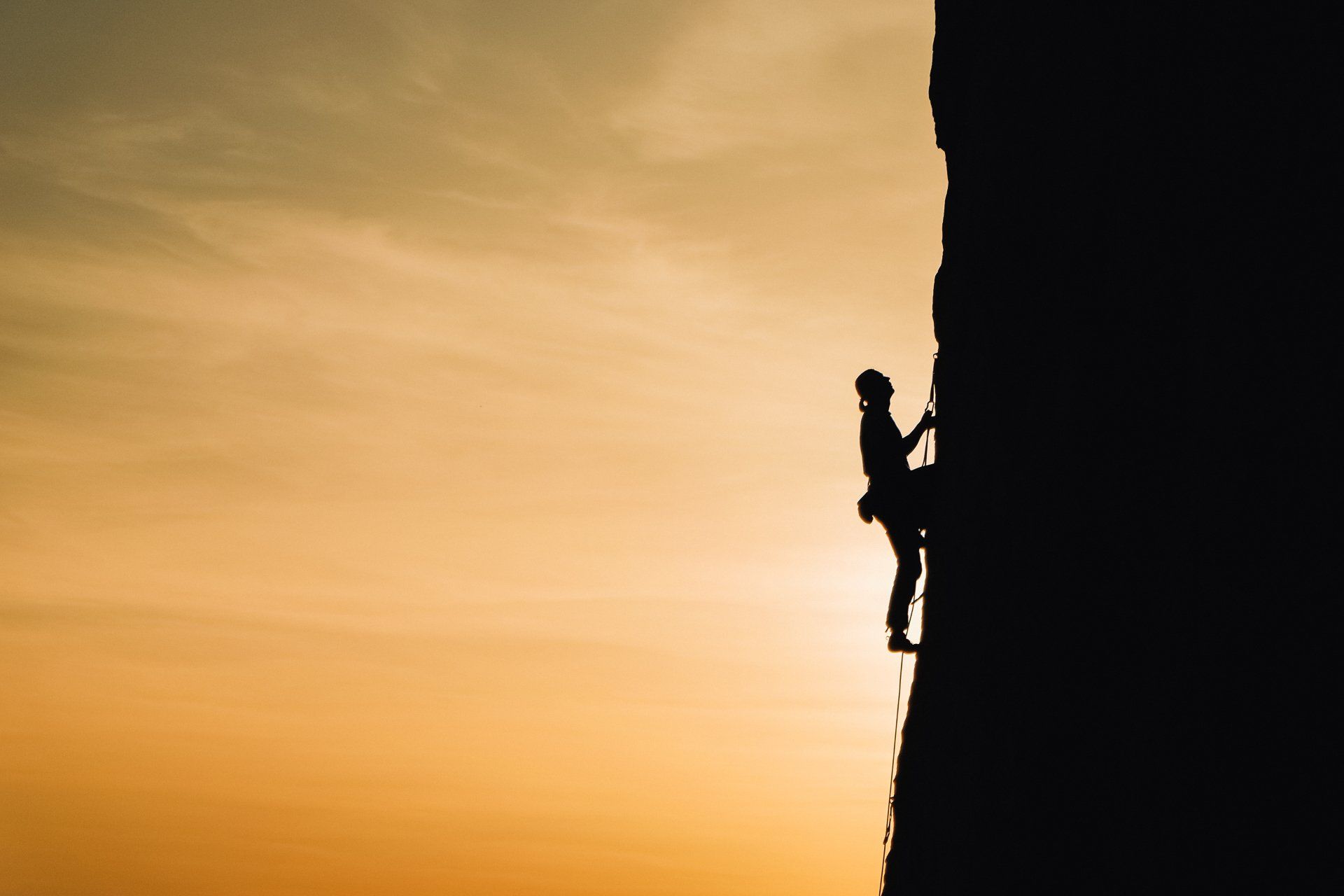
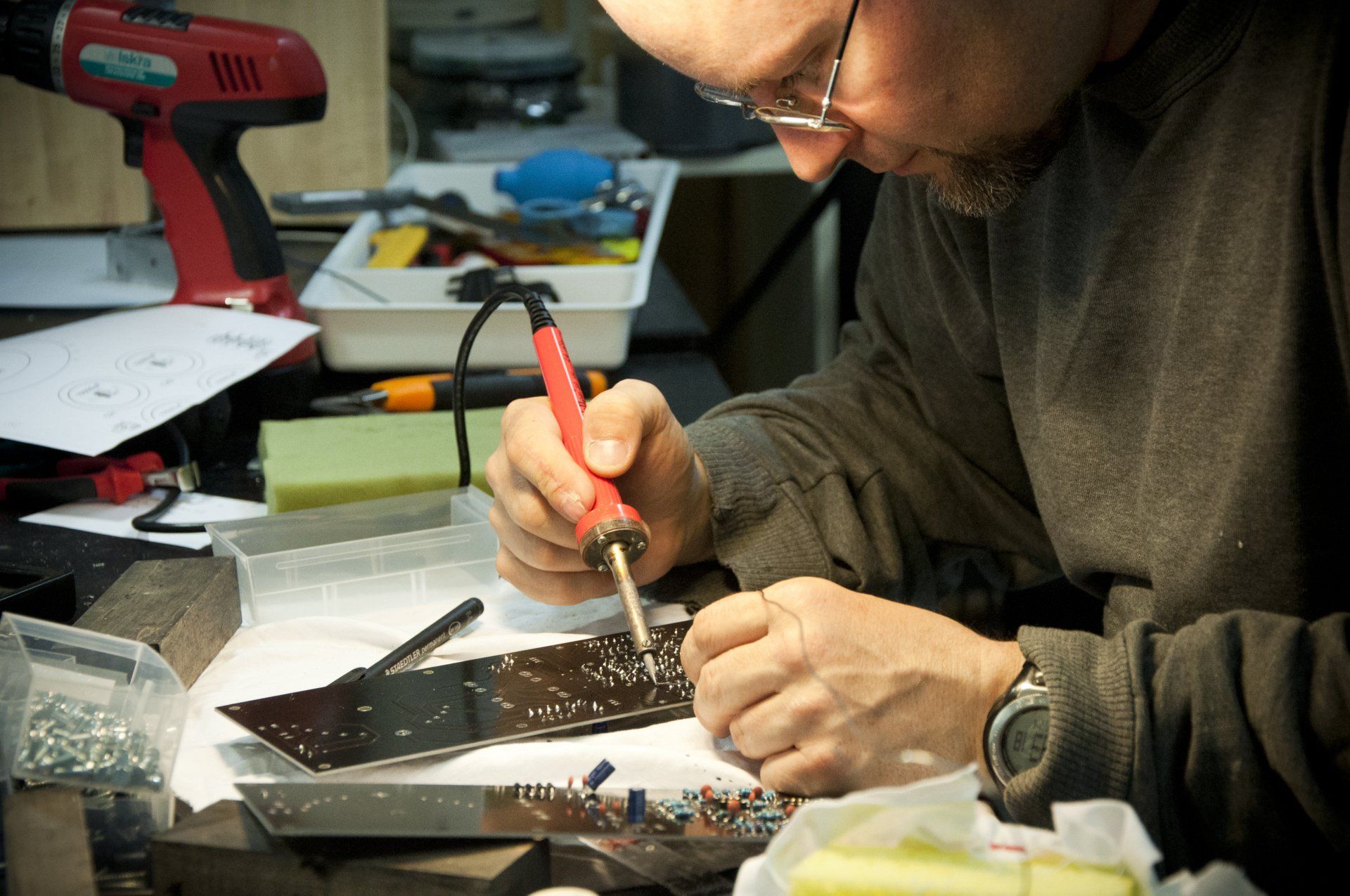
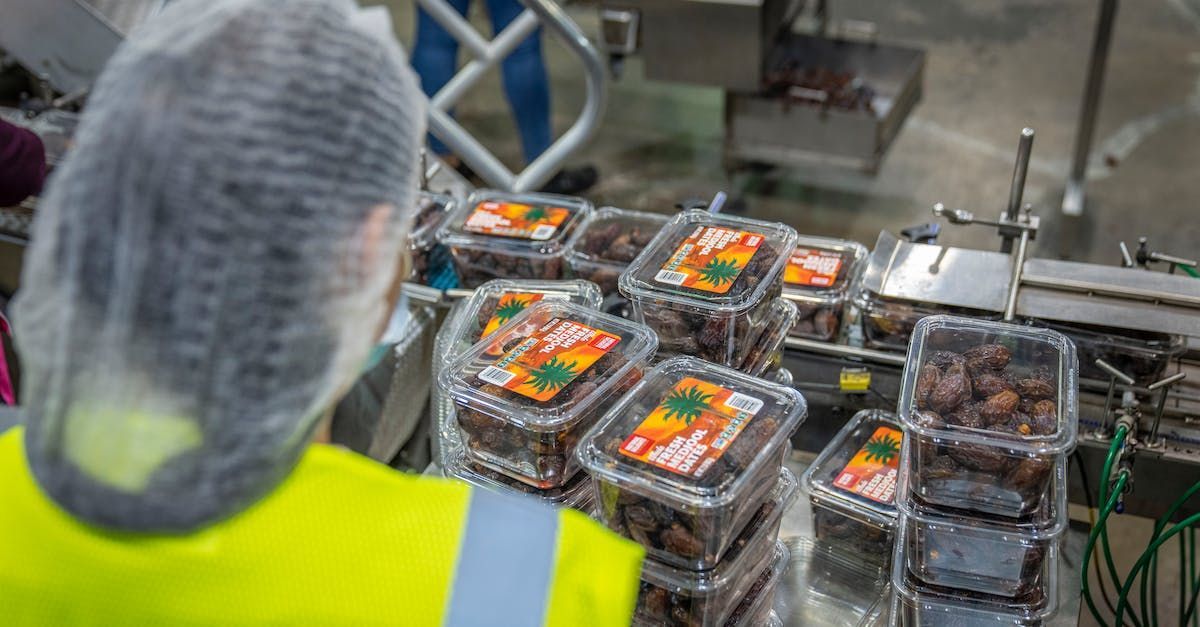
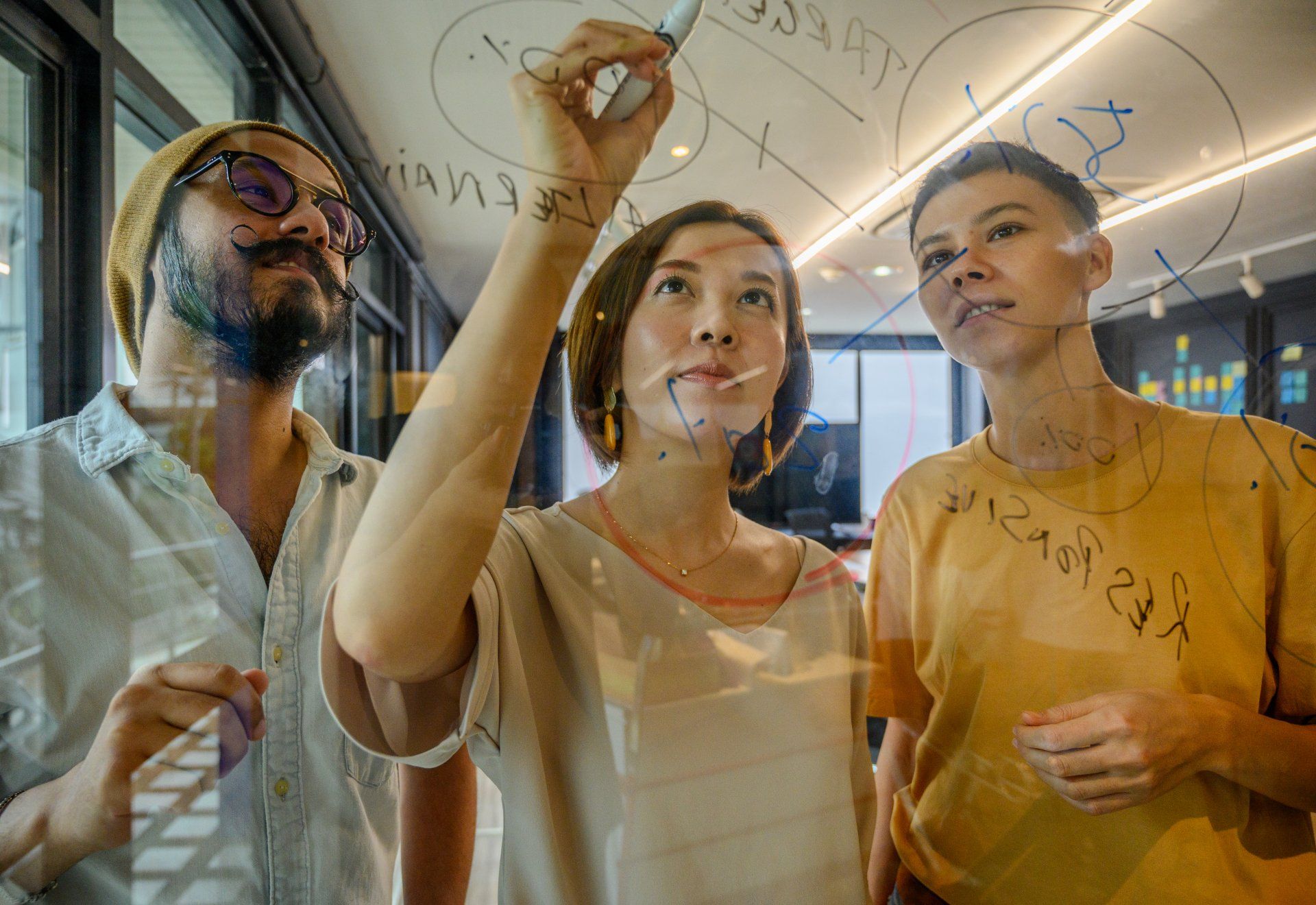
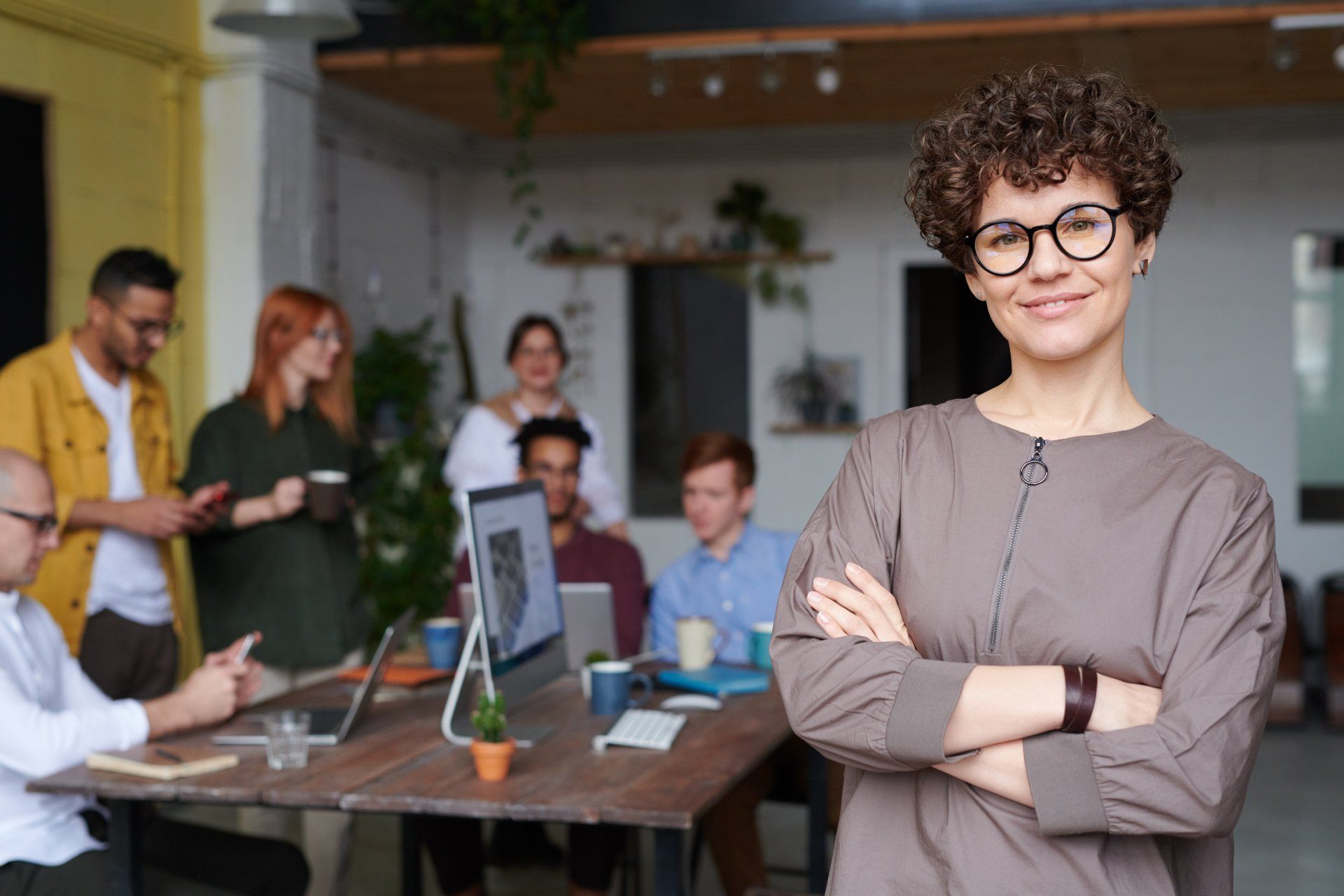
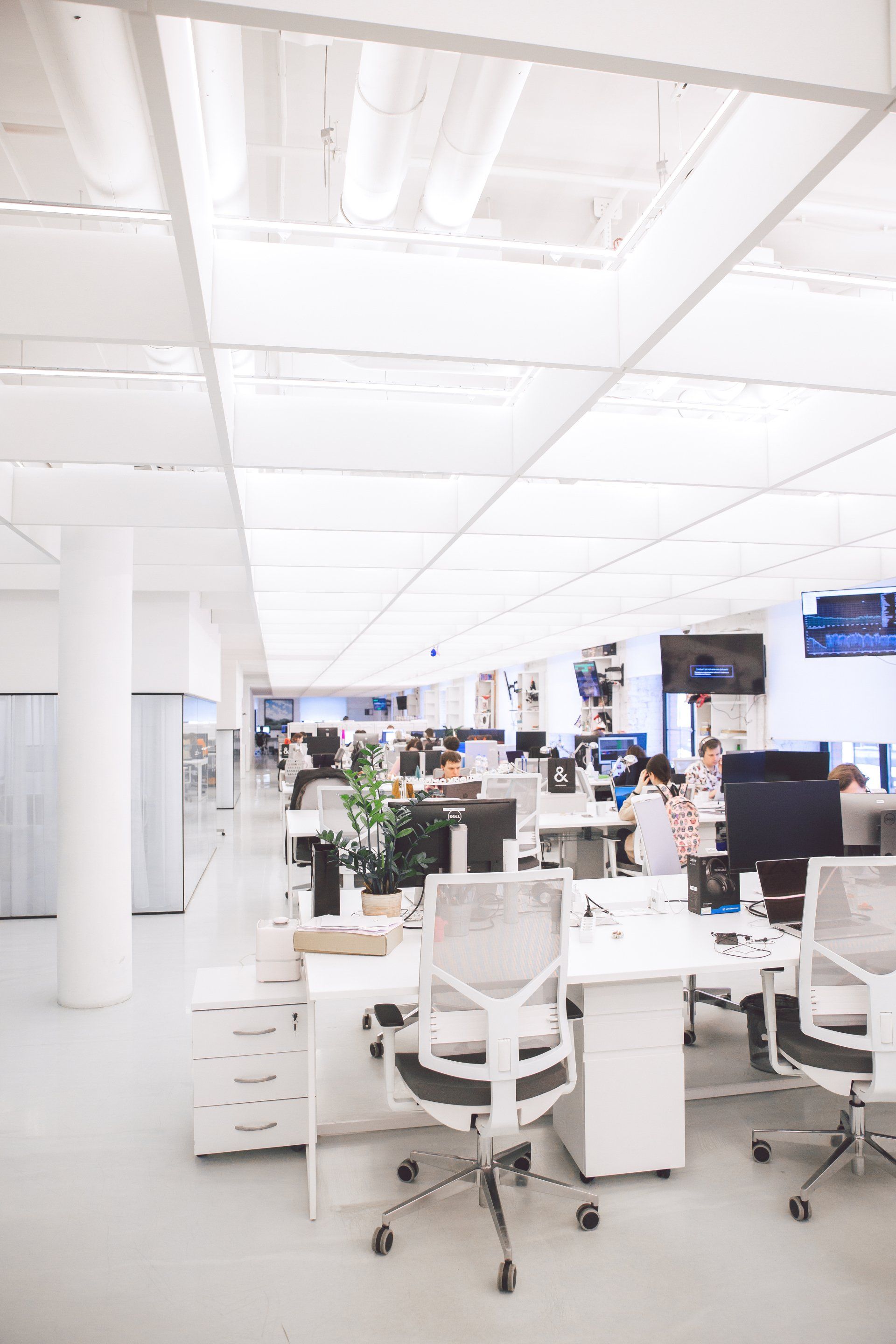