5S Methodology: Transforming Workspaces for Efficiency and Productivity
In today's fast-paced and competitive business environment, efficiency and productivity are crucial factors in achieving success. The 5S Methodology, rooted in Lean Thinking, offers a structured approach to organizing workspaces for optimal efficiency. Comprising five key principles—Sort, Set in Order, Shine, Standardize, and Sustain—5S helps organizations transform their work environments, reduce waste, and enhance productivity. In this comprehensive guide, we'll explore the principles of 5S and offer insights on how organizations can implement these practices for improved workplace organization and efficiency.
Understanding the 5S Methodology Principles
1. Sort (Seiri)
Sort involves the process of separating necessary items from unnecessary ones in the workspace. It's about decluttering and removing items that are not needed for current operations, reducing unnecessary inventory, tools, or materials.
2. Set in Order (Seiton)
Set in Order focuses on arranging and organizing necessary items in a structured and easily accessible manner. Everything should have a designated place, and tools and materials should be organized for efficient use, reducing time spent searching for items.
3. Shine (Seiso)
Shine refers to the practice of cleanliness and maintaining a tidy workspace. Regular cleaning and maintenance ensure that the workspace is free from dirt, clutter, and potential safety hazards.
4. Standardize (Seiketsu)
Standardize involves establishing clear, standardized procedures and practices for maintaining the first three S's. It ensures consistency in sorting, arranging, and cleanliness, setting clear guidelines for maintaining an organized workspace.
5. Sustain (Shitsuke)
Sustain is about ingraining the 5S principles into the organizational culture. It involves training, discipline, and continuous reinforcement to ensure that the improvements achieved through 5S are sustained over the long term.
Insights for Implementing 5S Practices
1. Create a 5S Implementation Team
Form a dedicated team responsible for leading the 5S implementation efforts. This team should consist of representatives from different departments to ensure diverse perspectives and active participation.
2. Conduct a 5S Assessment
Begin by assessing the current state of the workspace using the 5S principles. Identify areas that require improvement and prioritize actions based on their impact on efficiency and safety.
3. Sort: Declutter and Organize
Initiate the sorting process by identifying and eliminating unnecessary items in the workspace. Create designated storage areas and remove any items that do not contribute to immediate operations.
4. Set in Order: Organize for Efficiency
Arrange the remaining necessary items in a structured manner. Utilize visual aids such as labels, colour-coding, and shadow boards to make tools and materials easily identifiable and accessible.
5. Shine: Clean and Maintain
Implement regular cleaning schedules to maintain cleanliness in the workspace. Encourage employees to take ownership of cleanliness and perform routine checks for maintenance.
6. Standardize: Establish Procedures
Develop and document standardized procedures for sorting, arranging, and cleaning. Ensure that these procedures are clearly communicated and easily accessible to all employees.
7. Sustain: Foster a Culture of Continuous Improvement
Promote employee involvement and ownership of the 5S practices. Provide training, conduct regular audits, and recognize and reward individuals or teams for maintaining 5S standards.
Benefits of Implementing 5S Methodology
1. Improved Efficiency and Productivity
Implementing 5S practices streamlines workflows, reduces time spent searching for tools or information, and enhances overall operational efficiency.
2. Enhanced Safety and Reduced Waste
A clean and organized workspace reduces the risk of accidents and injuries. Additionally, eliminating unnecessary items minimizes waste and optimizes resources.
3. Increased Employee Morale and Engagement
A well-organized and clean workspace creates a more pleasant working environment, boosting employee morale and fostering a sense of pride in their work.
4. Better Quality and Standardization
Standardized procedures and organized workspaces contribute to better quality control and consistency in operations.
Real-Life Examples of 5S Implementation
Example 1: Automotive Manufacturing
Automotive manufacturers often use 5S principles to organize assembly lines, ensuring tools, parts, and equipment are readily accessible to workers, reducing assembly time and errors.
Example 2: Healthcare Facilities
Hospitals and healthcare facilities implement 5S to ensure cleanliness, organize medical supplies, and reduce the risk of errors in patient care by having a structured and efficient workspace.
Conclusion
The 5S Methodology offers a systematic approach to organizing workspaces for improved efficiency, productivity, and safety. By implementing the principles of Sort, Set in Order, Shine, Standardize, and Sustain, organizations can transform their work environments, reduce waste, and foster a culture of continuous improvement. Embracing the 5S Methodology not only enhances operational efficiency but also contributes to a more engaged and motivated workforce, ultimately driving success in today's competitive business landscape.
Understanding Lean Thinking: 5 Key Principles Explained and Applied
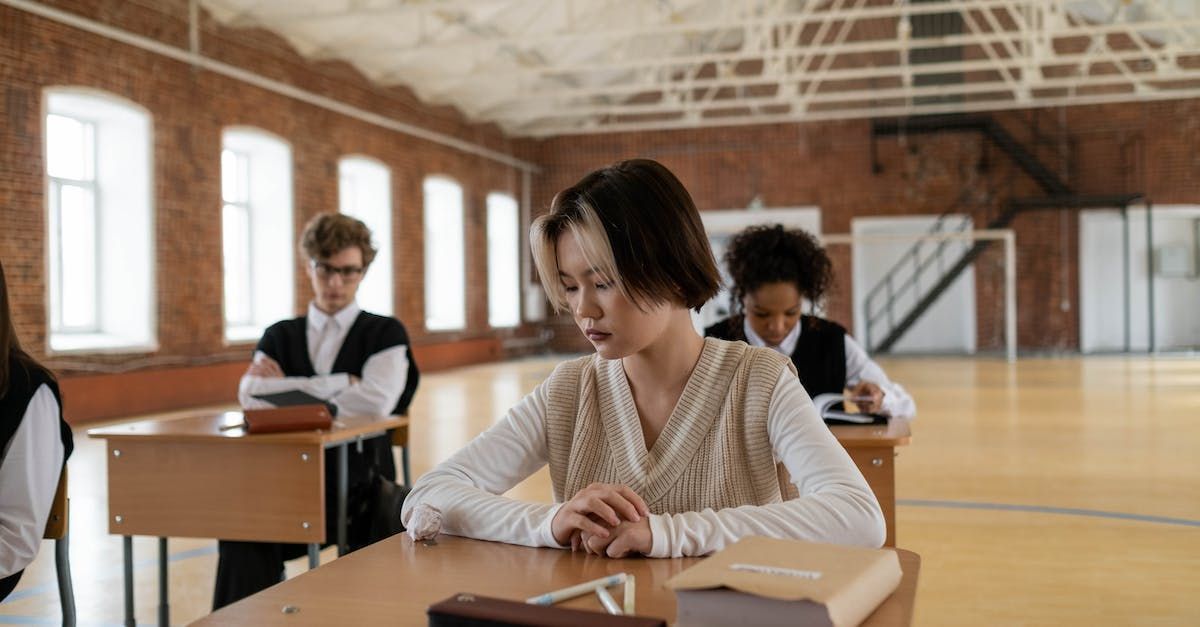
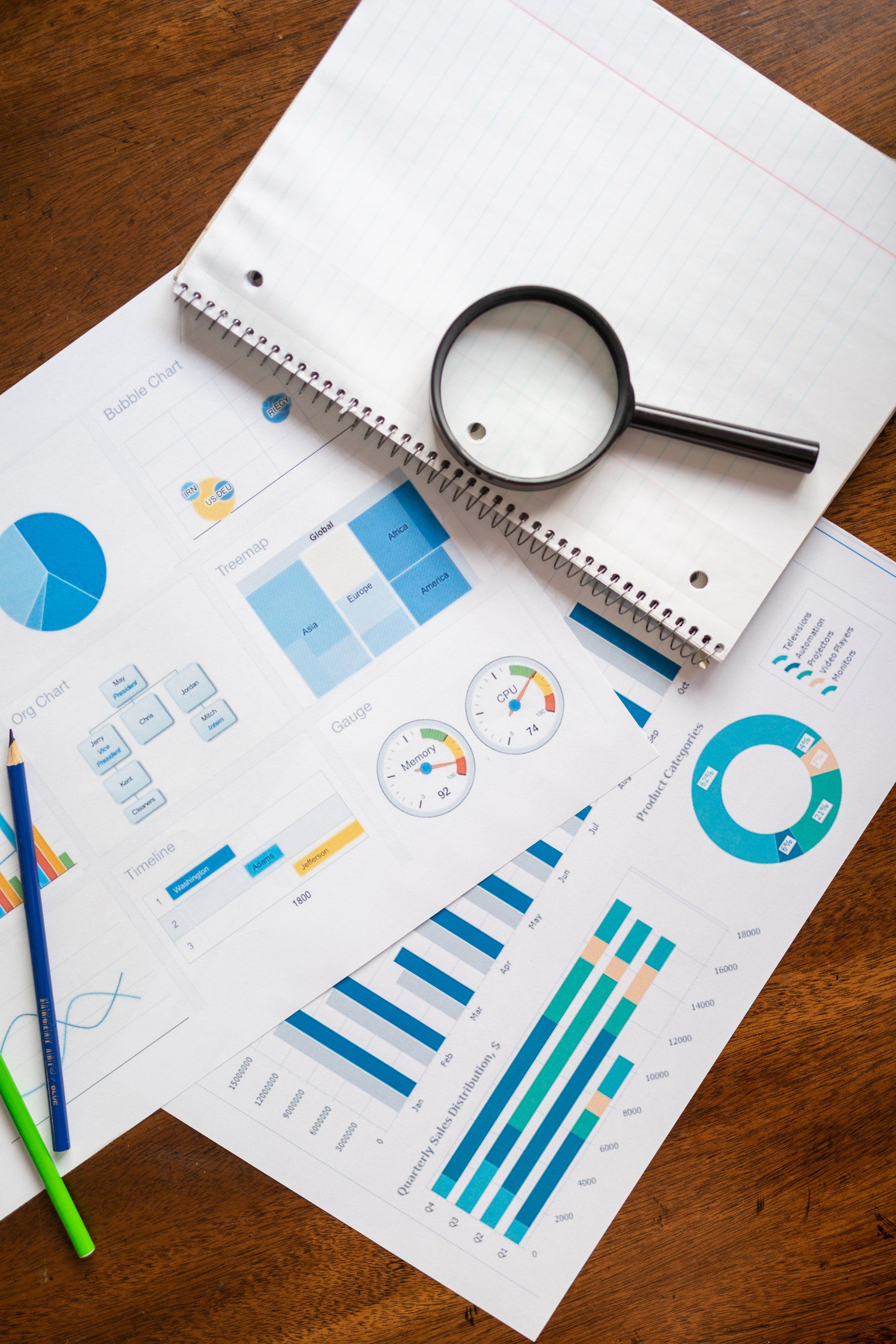
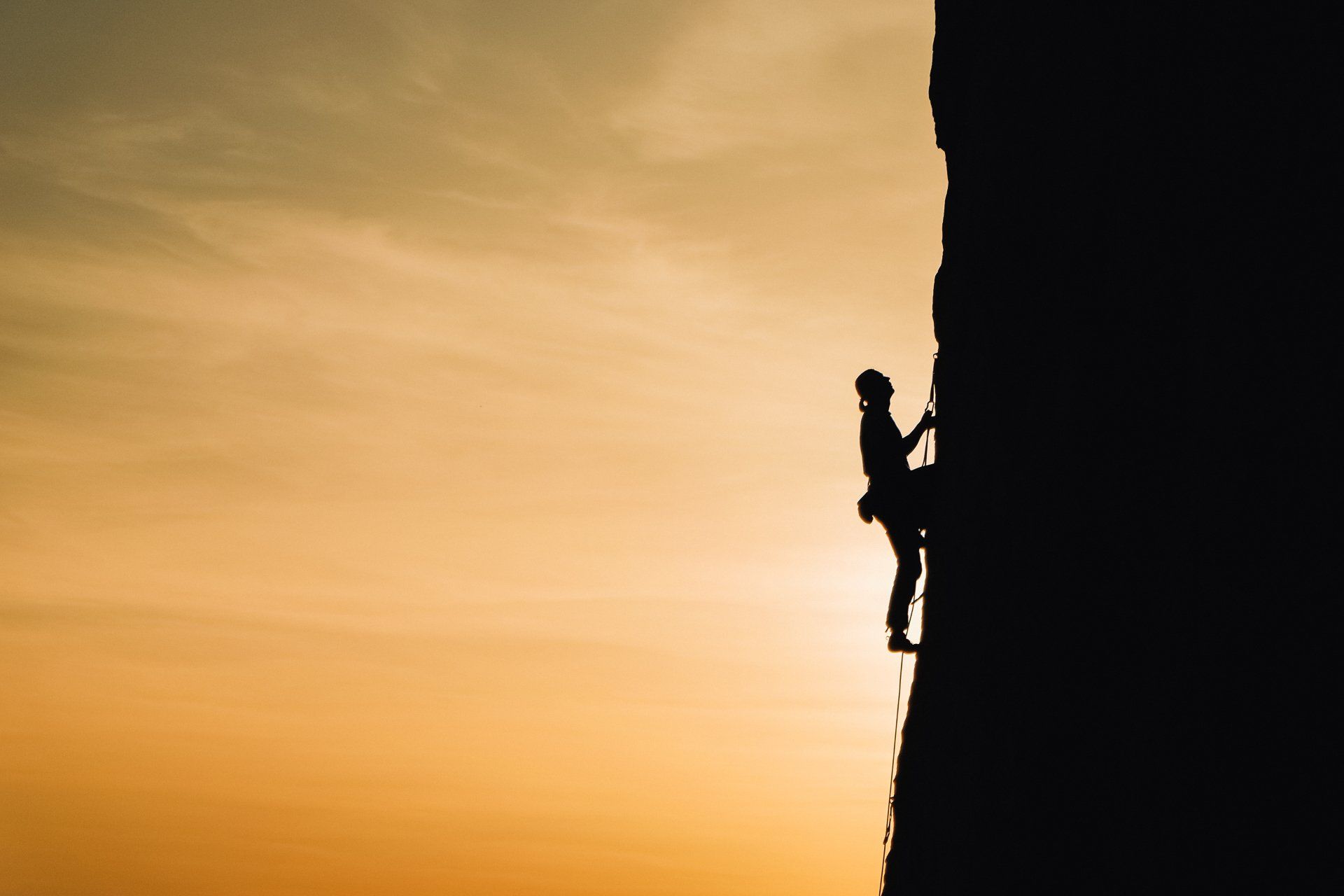
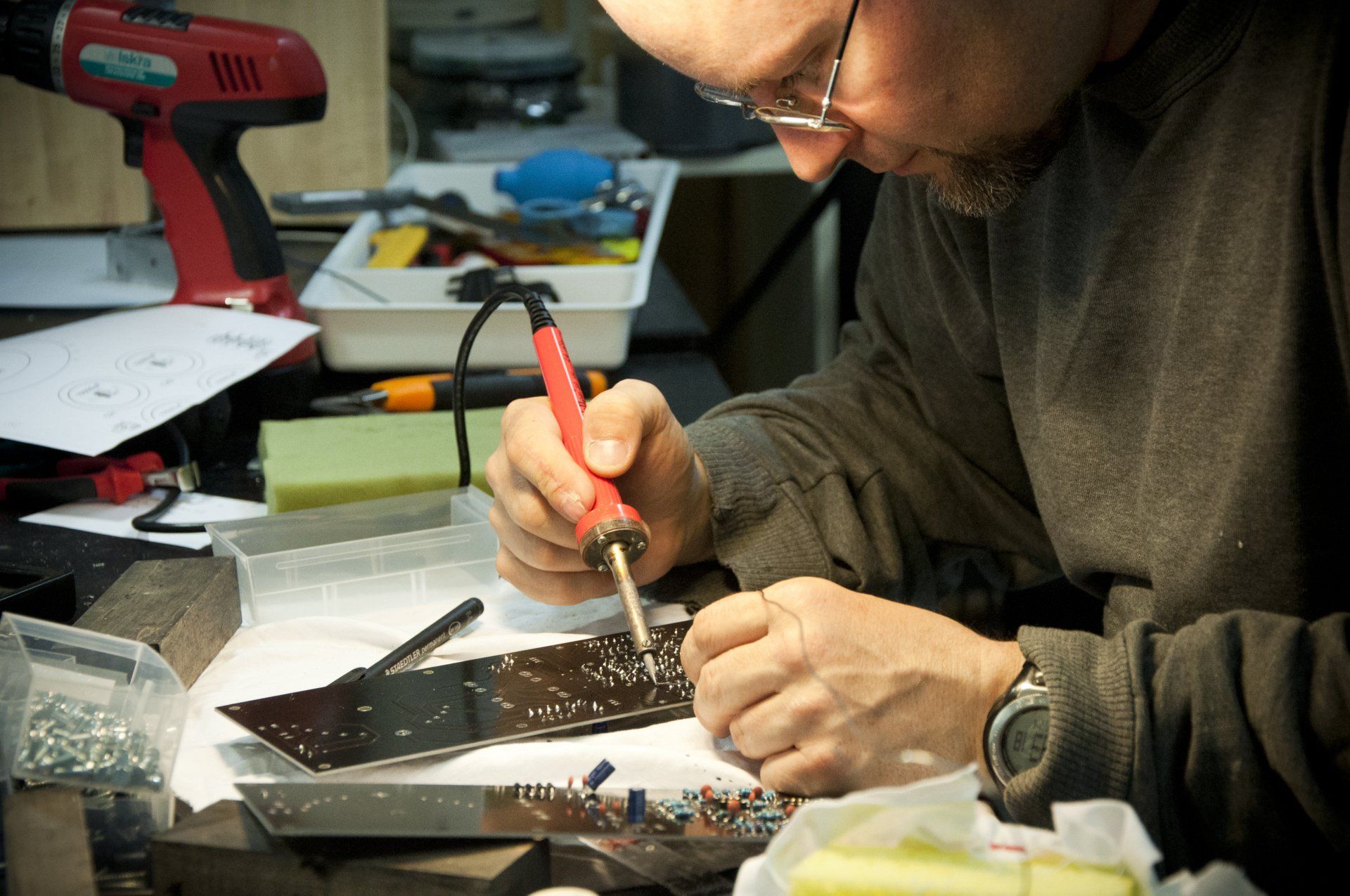
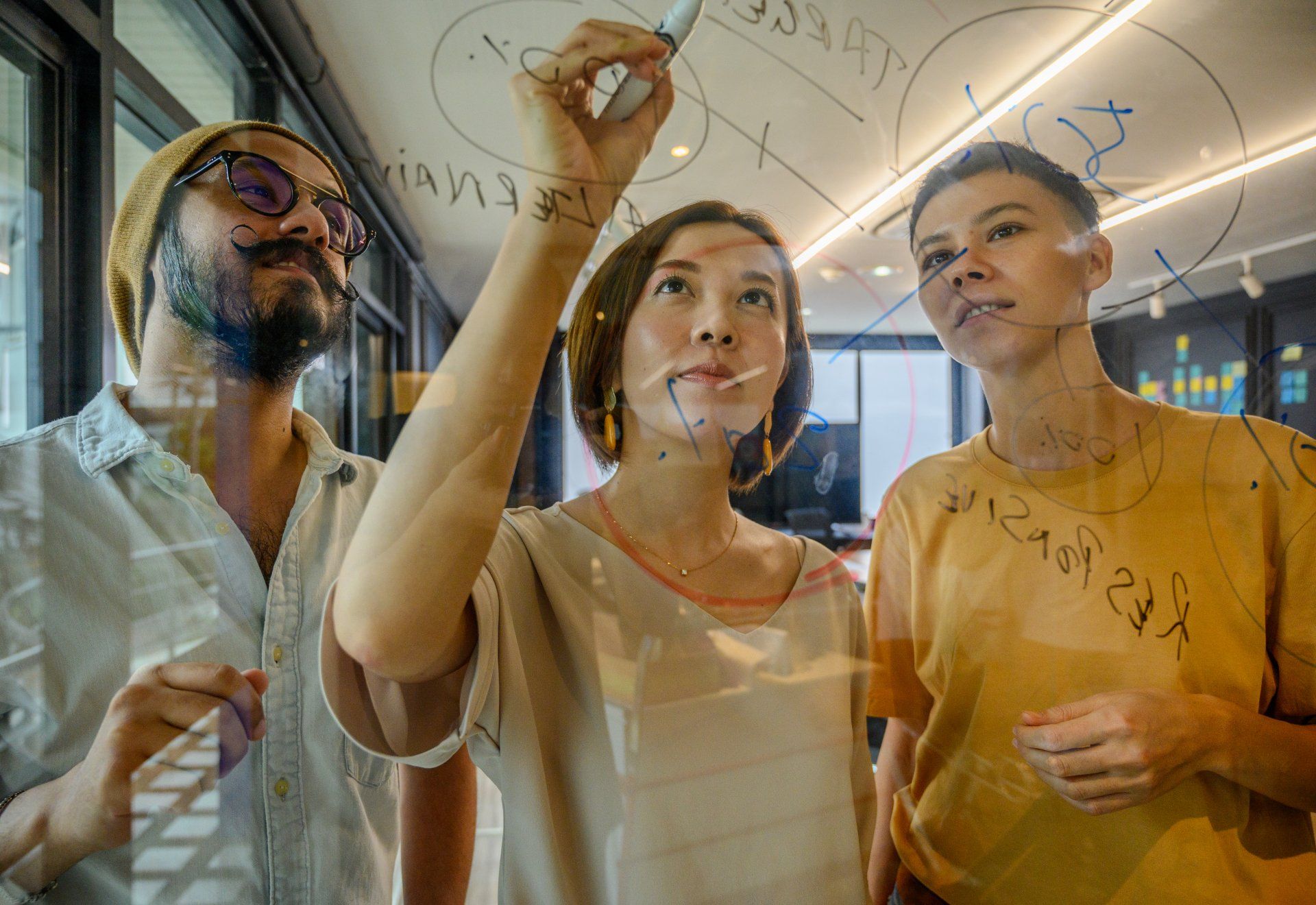
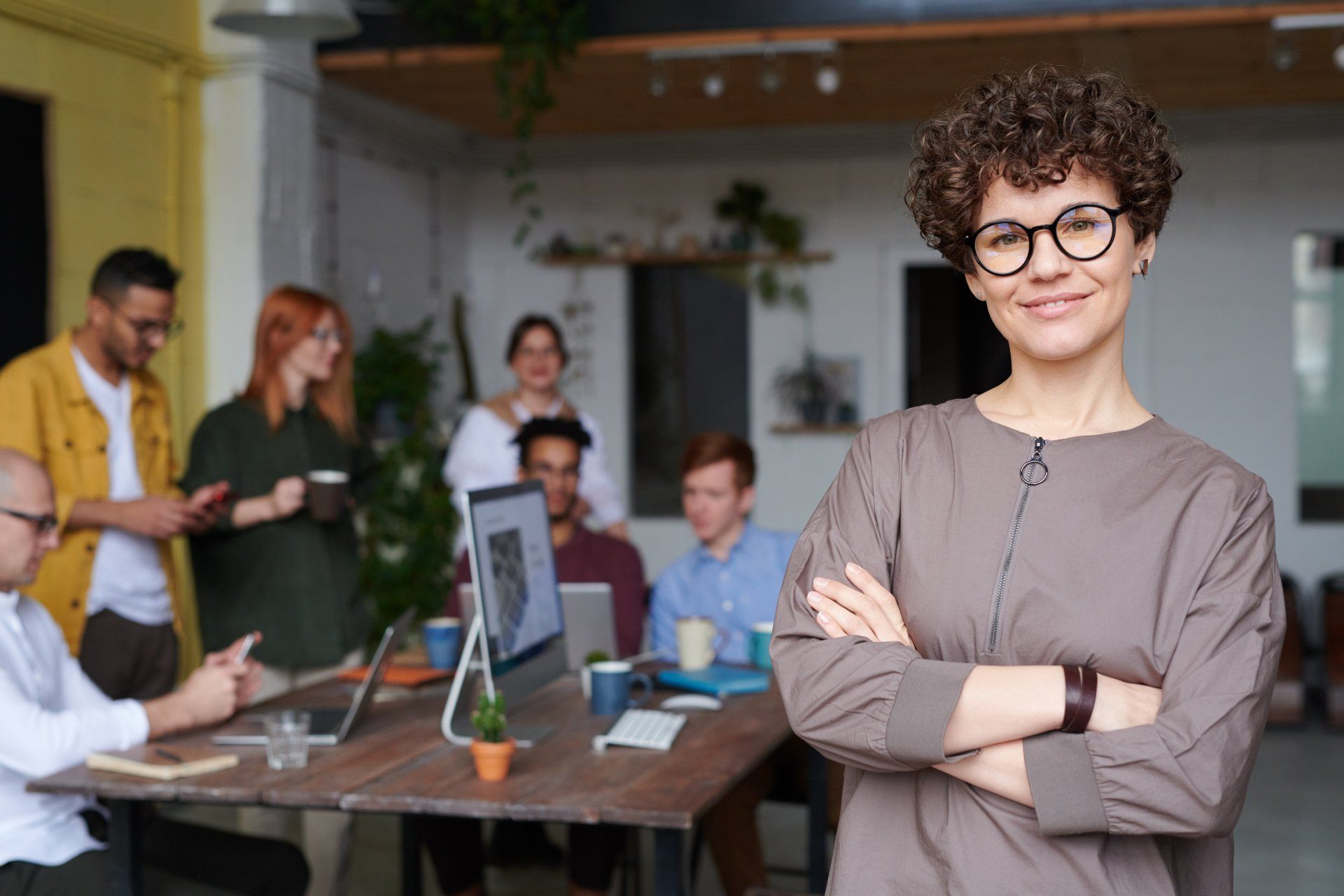
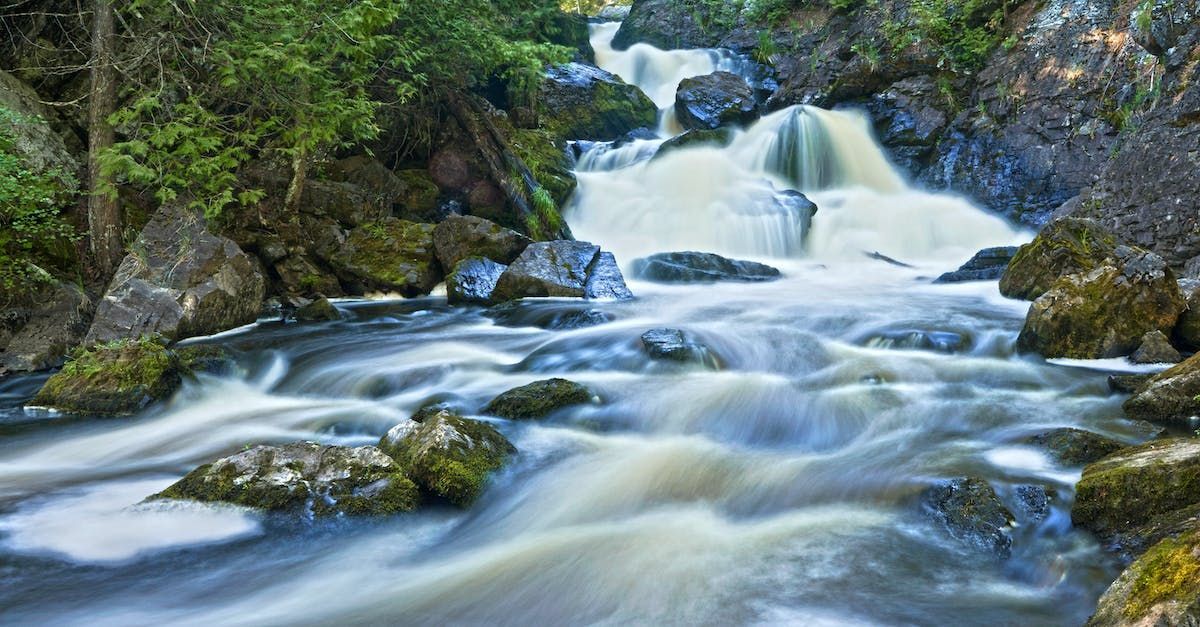
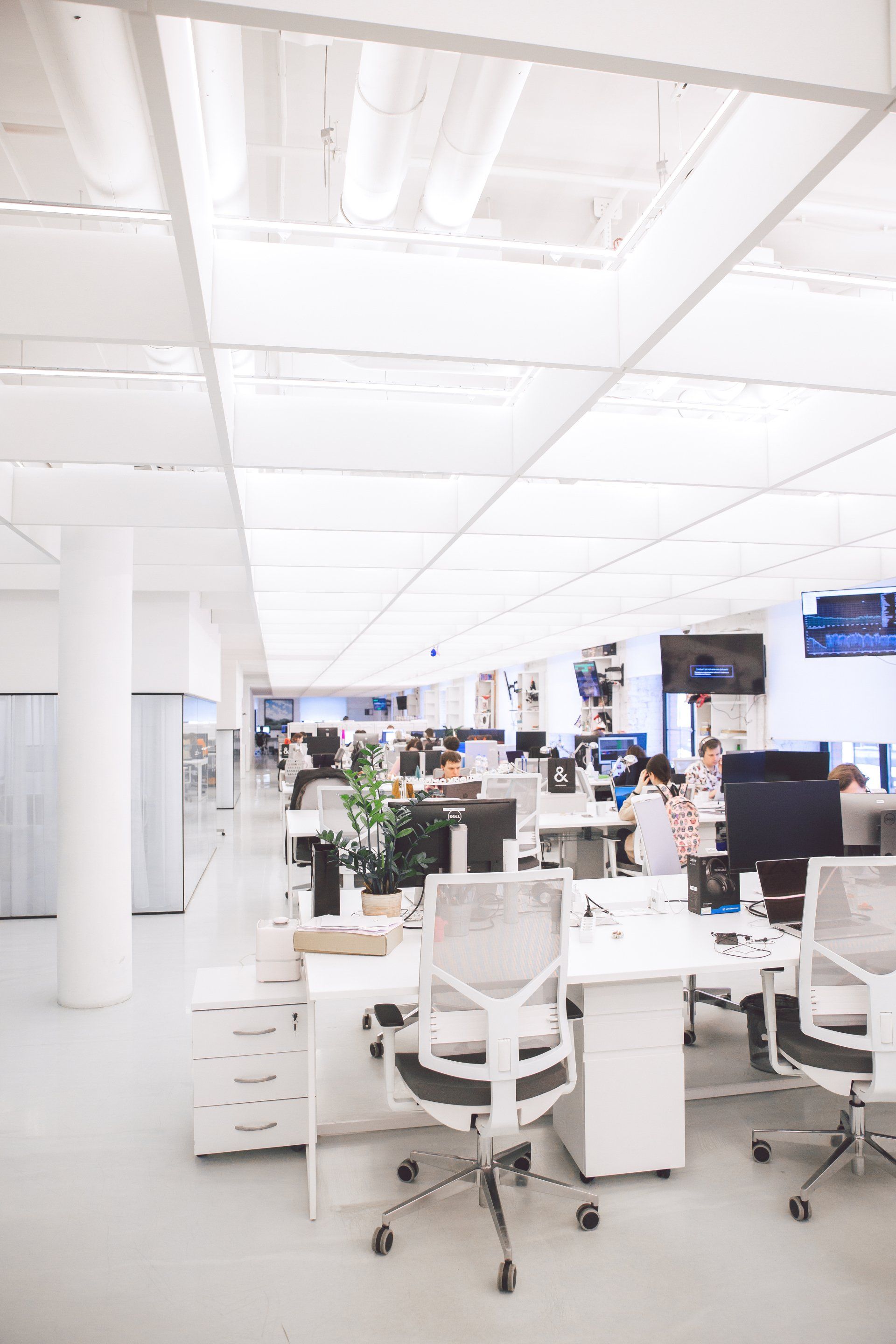