Overcoming Common Challenges in Lean Implementation and Sustaining Results
Implementing Lean methodologies is a journey toward operational excellence, marked by significant benefits such as improved efficiency, reduced waste, and enhanced productivity. However, organizations often face various challenges during Lean implementation that can hinder progress and sustainability. In this comprehensive guide, we'll address common obstacles encountered in Lean implementation and offer strategies to overcome these challenges while maintaining long-term success.
Common Challenges in Lean Implementation
1. Lack of Leadership Commitment
One of the primary challenges is inadequate commitment and support from organizational leadership. Without strong sponsorship, initiatives may lack direction and fail to gain traction among employees.
2. Resistance to Change
Resistance from employees accustomed to existing workflows is another hurdle. Introducing Lean often disrupts established routines, leading to resistance and reluctance to embrace new processes.
3. Inadequate Training and Skill Gaps
Insufficient training and a lack of expertise in Lean methodologies among employees can impede successful implementation. Without proper knowledge, individuals may struggle to adapt to new practices.
4. Failure to Sustain Improvements
Sustaining the improvements achieved through Lean initiatives poses a challenge. Without continuous monitoring and reinforcement, organizations may regress to previous inefficient practices.
Strategies to Overcome Lean Implementation Challenges
1. Foster Strong Leadership Commitment
Ensure top-level commitment by engaging leaders in the Lean journey. Leaders should actively communicate the vision, provide resources, and actively participate in Lean initiatives.
2. Cultivate a Culture of Continuous Improvement
Promote a culture that encourages and values continuous improvement. Engage employees by soliciting their input, recognizing their contributions, and fostering a sense of ownership in Lean initiatives.
3. Provide Comprehensive Training and Support
Offer extensive training and support to employees at all levels. Develop a structured training program to equip them with the knowledge and skills needed for successful Lean adoption.
4. Address Resistance through Communication
Proactively address resistance by communicating the rationale behind Lean initiatives. Engage employees in dialogue, address concerns, and highlight the benefits of Lean for both the organization and individuals.
5. Prioritize Change Management
Implement robust change management practices to navigate resistance effectively. Involve change champions, provide adequate resources, and communicate the importance of change adoption.
Sustaining Lean Success in the Long Run
1. Establish Key Performance Indicators (KPIs)
Define measurable KPIs to track progress and success. Regularly monitor and analyze performance metrics to ensure that improvements are sustained and aligned with organizational goals.
2. Implement Continuous Monitoring and Improvement
Create a system for continuous monitoring and improvement. Regularly review processes, gather feedback, and iterate on Lean initiatives to adapt to changing needs and maintain momentum.
3. Empower and Engage Employees
Empower employees by involving them in decision-making and improvement initiatives. Encourage their participation, provide opportunities for skill development, and recognize their contributions.
4. Standardize and Document Best Practices
Document successful Lean practices and create standardized procedures. Establish guidelines and protocols to ensure consistency and sustainability across the organization.
5. Celebrate Achievements and Share Success Stories
Acknowledge and celebrate achievements resulting from Lean initiatives. Share success stories across the organization to inspire and motivate employees to sustain their efforts.
Real-Life Examples of Overcoming Lean Challenges
Example 1: Toyota's Approach to Leadership Commitment
Toyota's success in Lean implementation is attributed to strong leadership commitment. Executives actively engage in Gemba Walks, demonstrating their commitment to Lean principles and fostering a culture of continuous improvement.
Example 2: GE's Continuous Improvement Culture
General Electric (GE) focuses on building a culture of continuous improvement by providing extensive training to employees. They invest in Lean Six Sigma initiatives, empowering employees to drive and sustain improvement.
Conclusion
Lean implementation presents numerous challenges that organizations must address to achieve sustained success. Overcoming these obstacles requires strong leadership commitment, employee engagement, comprehensive training, and a continuous improvement mindset. By fostering a culture that values Lean principles, implementing robust change management practices, and establishing mechanisms for continuous monitoring and improvement, organizations can overcome challenges and sustain long-term success with Lean methodologies.
Understanding Lean Thinking: 5 Key Principles Explained and Applied
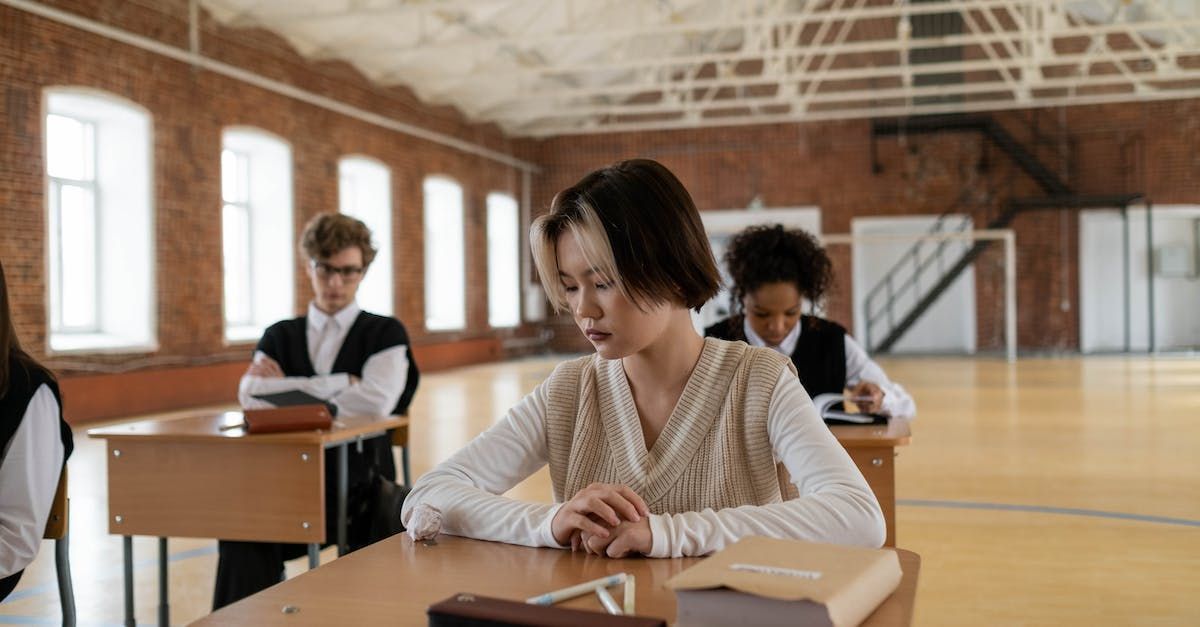
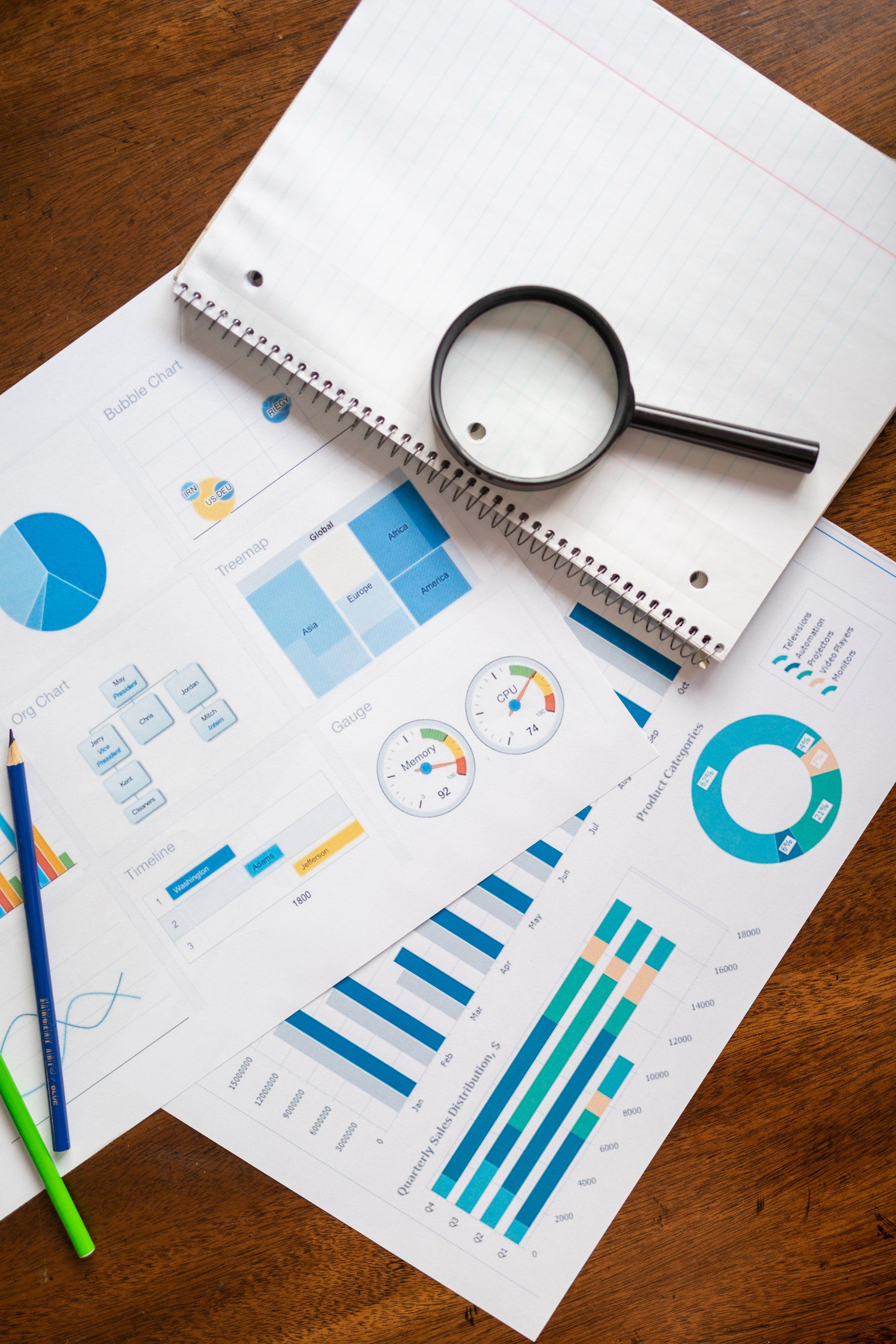
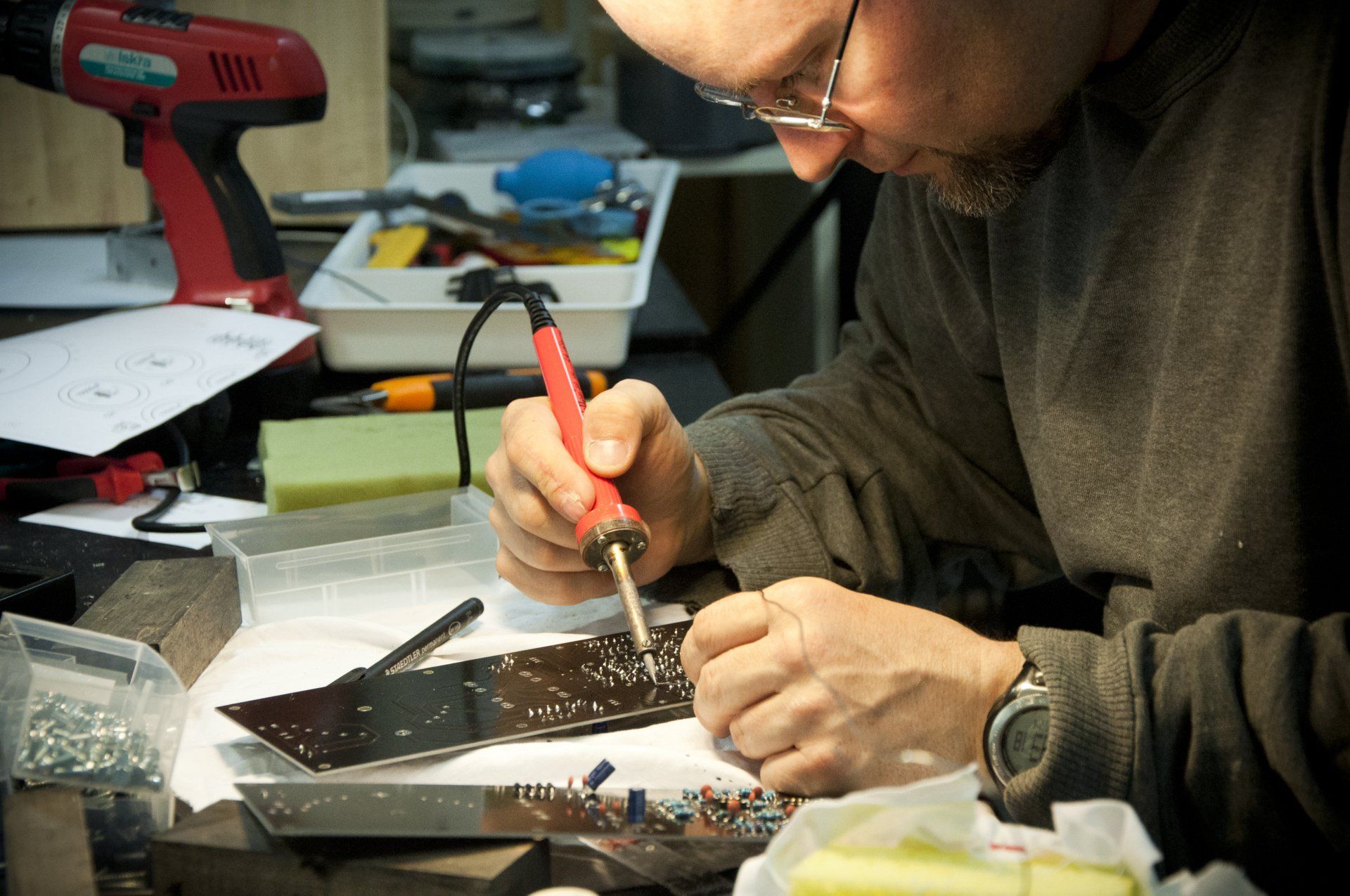
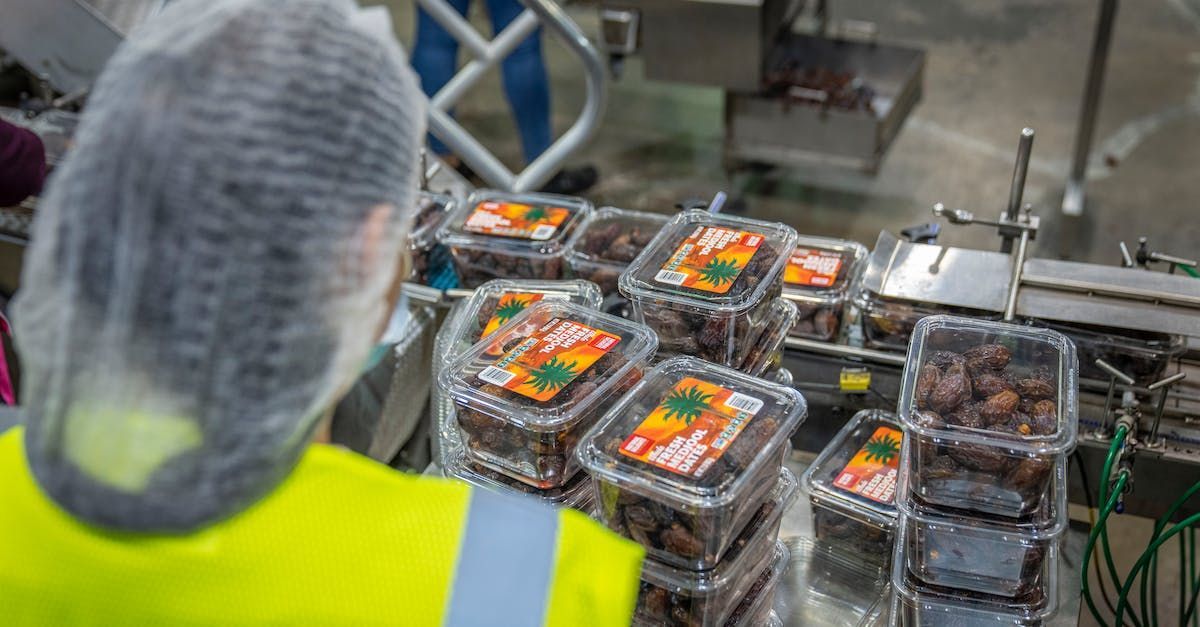
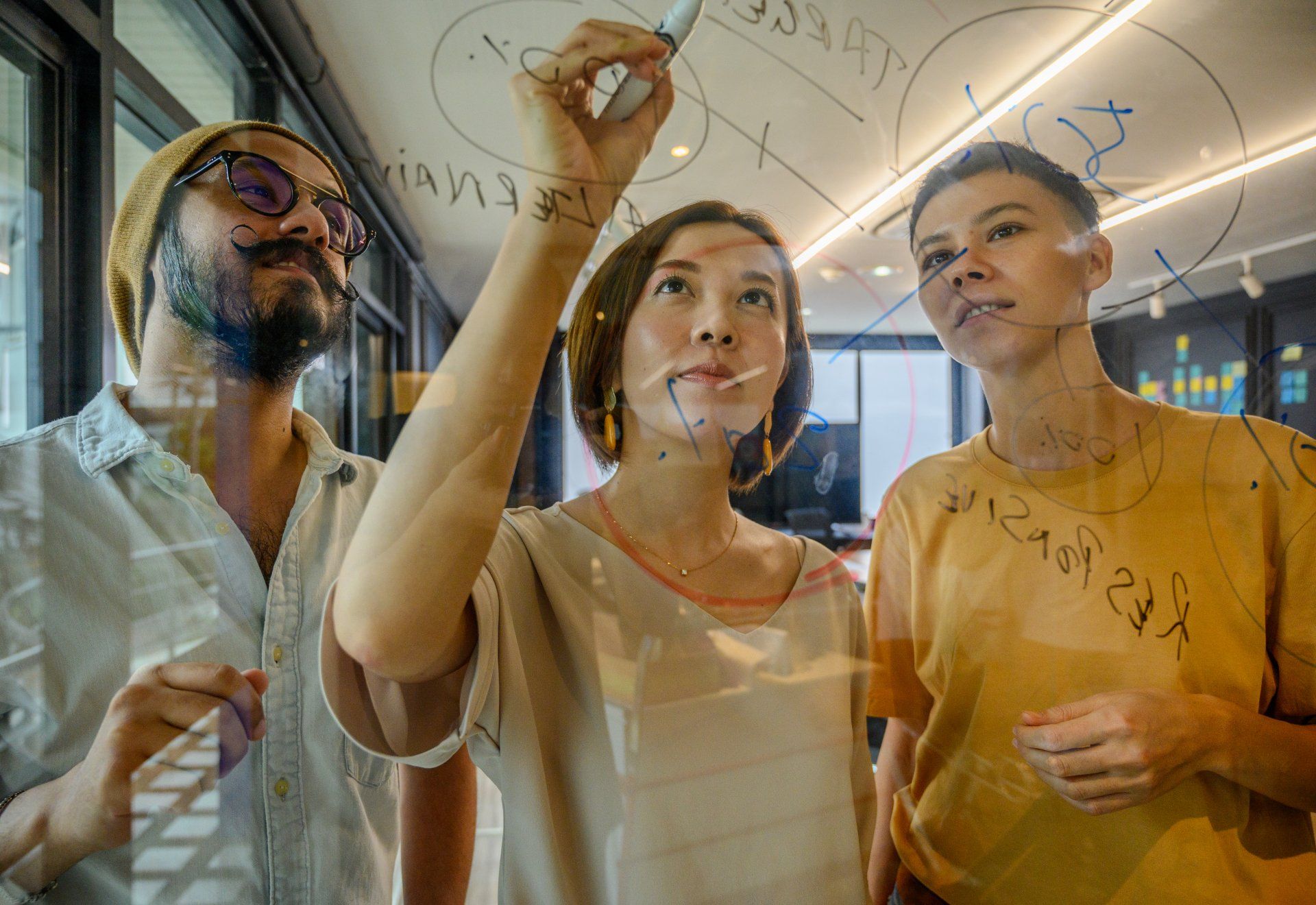
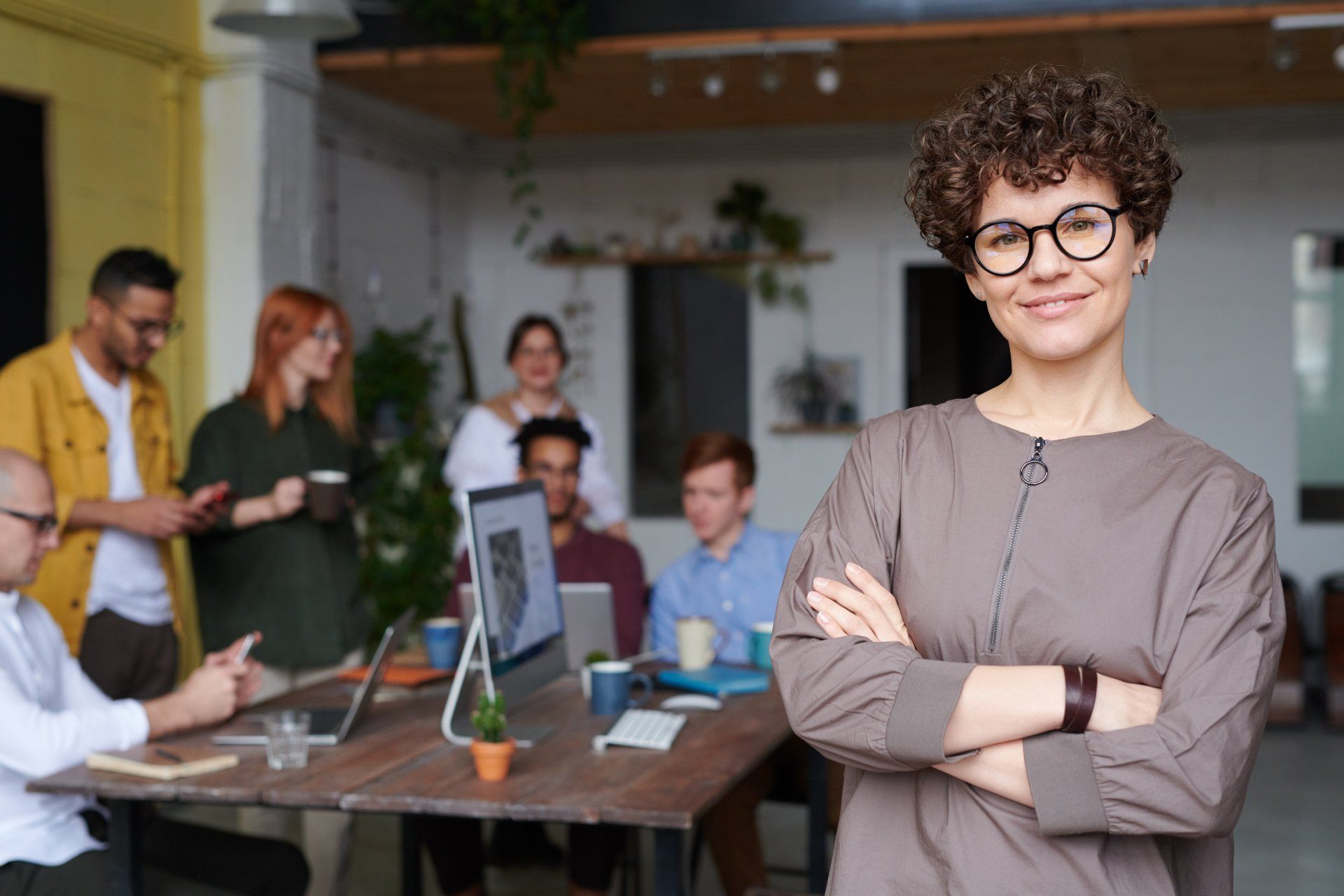
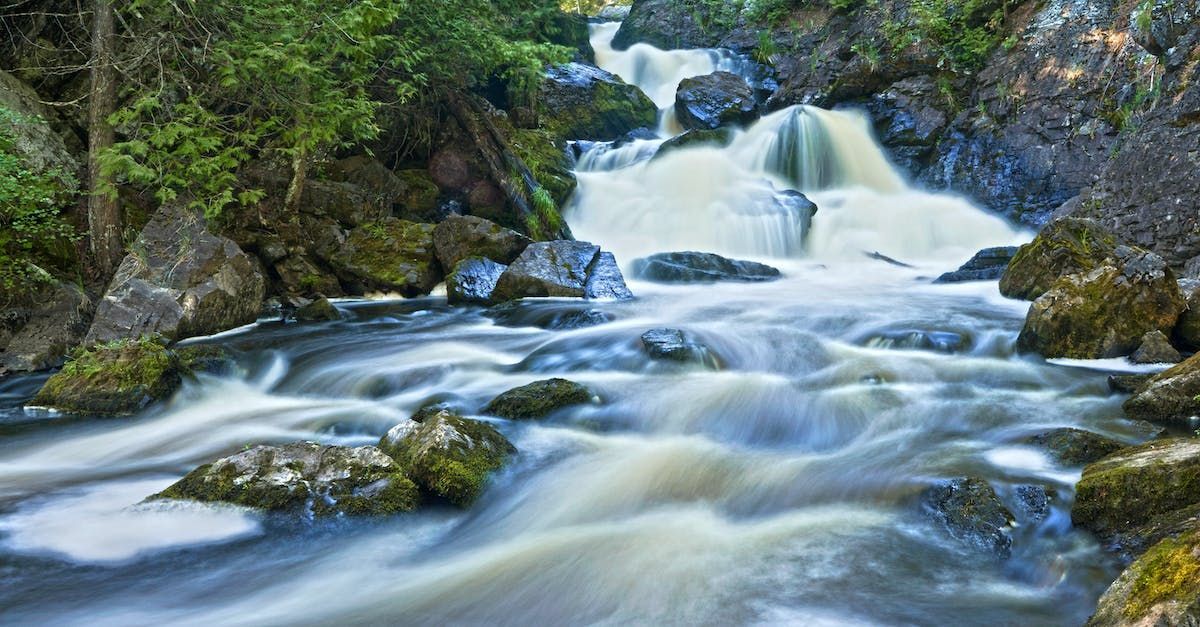
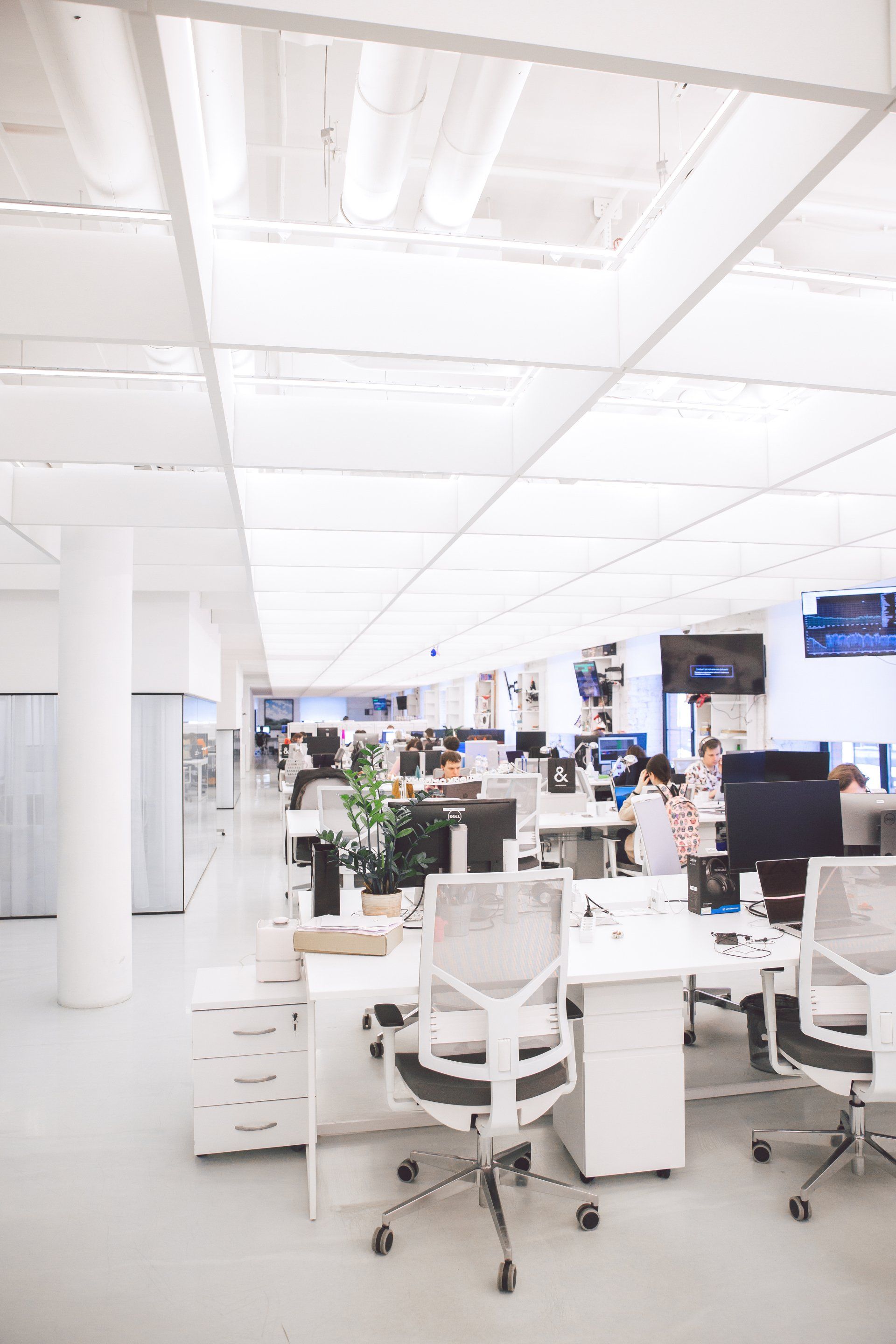