Measuring Lean Success: Key Metrics and KPIs to Track Improvement
Implementing Lean methodologies within an organization is not just about making changes; it's about driving continuous improvement and achieving tangible results. To effectively gauge the impact of Lean initiatives and ensure progress aligns with organizational objectives, measuring success through Key Performance Indicators (KPIs) is imperative. In this comprehensive guide, we'll discuss the importance of measuring Lean success and provide a list of essential KPIs to monitor progress effectively.
The Importance of Measuring Lean Success
1. Assessing Effectiveness
Measuring Lean success allows organizations to assess the effectiveness of implemented initiatives. It provides insights into whether the changes made have positively impacted processes, productivity, and efficiency.
2. Identifying Improvement Areas
Tracking KPIs helps identify specific areas that require further improvement. It highlights bottlenecks, inefficiencies, or areas where Lean principles might not have been fully integrated.
3. Monitoring Progress Toward Goals
KPIs serve as benchmarks for progress toward organizational goals. Regularly measuring success ensures initiatives remain aligned with overall objectives and strategic direction.
4. Enhancing Decision-Making
Data-driven insights from KPIs facilitate informed decision-making. Leaders can use this information to prioritize resources and make strategic adjustments to optimize Lean initiatives.
Essential KPIs for Measuring Lean Success
1. Lead Time
Lead time measures the time taken for a product or service to move through the entire process—from initiation to delivery. Reducing lead time indicates improved efficiency and responsiveness to customer demands.
2. Cycle Time
Cycle time refers to the time required to complete a single unit of work within a process. Decreasing cycle time signifies enhanced productivity and streamlined workflows.
3. Overall Equipment Effectiveness (OEE)
OEE measures equipment utilization, performance, and quality. It helps identify equipment downtime, inefficiencies, and opportunities for improvement in manufacturing processes.
4. Defect Rate
Defect rate calculates the percentage of defective products or services. Lower defect rates indicate higher quality and improved process reliability.
5. Inventory Turnover
Inventory turnover measures how quickly inventory is used or sold within a specific period. Higher turnover rates suggest efficient inventory management and reduced waste.
6. Cost of Quality (COQ)
COQ evaluates the total cost incurred due to poor quality, including prevention, appraisal, internal failure, and external failure costs. Lower COQ signifies improved quality and reduced waste.
7. Employee Engagement and Participation
Monitoring employee engagement and participation levels in Lean initiatives provides insights into the adoption and success of Lean practices within the workforce.
8. Value Stream Mapping (VSM) Improvements
Assessing improvements identified through Value Stream Mapping exercises helps track progress in eliminating waste and enhancing value-added activities.
9. Gemba Walk Findings
Regular Gemba Walks and the subsequent findings serve as indicators of frontline employee involvement, process visibility, and opportunities for improvement.
10. Customer Satisfaction
Measuring customer satisfaction or Net Promoter Score (NPS) reflects the impact of Lean initiatives on delivering value to customers and meeting their needs effectively.
Strategies for Effective Measurement of Lean KPIs
1. Define Clear Objectives and Targets
Establish specific objectives and targets for each KPI aligned with organizational goals. Clear benchmarks ensure focused efforts toward measurable improvements.
2. Utilize Technology and Data Analytics
Leverage technology and data analytics tools to collect, analyze, and visualize KPI data effectively. Dashboards and reporting tools facilitate easy tracking and monitoring.
3. Regularly Review and Benchmark
Regularly review KPIs to track progress and compare against industry benchmarks or best practices. Continuous monitoring allows for timely adjustments and improvements.
4. Engage Employees in Measurement Efforts
Involve employees in tracking and understanding KPIs relevant to their areas. Encourage ownership and participation in achieving improvement targets.
Real-Life Application of Lean KPIs
Example 1: Toyota's Focus on OEE
Toyota emphasizes OEE to measure manufacturing equipment effectiveness. They continuously monitor OEE metrics to identify and address inefficiencies, optimizing production processes.
Example 2: Amazon's Emphasis on Customer Satisfaction
Amazon uses customer satisfaction metrics as a key indicator of Lean success. They prioritize customer-centric KPIs to improve service quality and delivery performance.
Conclusion
Measuring Lean success through Key Performance Indicators (KPIs) is essential for organizations committed to continuous improvement. The identified KPIs serve as crucial metrics to evaluate the impact of Lean initiatives, identify improvement areas, and ensure alignment with organizational goals. By effectively tracking these KPIs, organizations can gauge progress, drive efficiencies, and sustain long-term success through Lean methodologies.
Understanding Lean Thinking: 5 Key Principles Explained and Applied
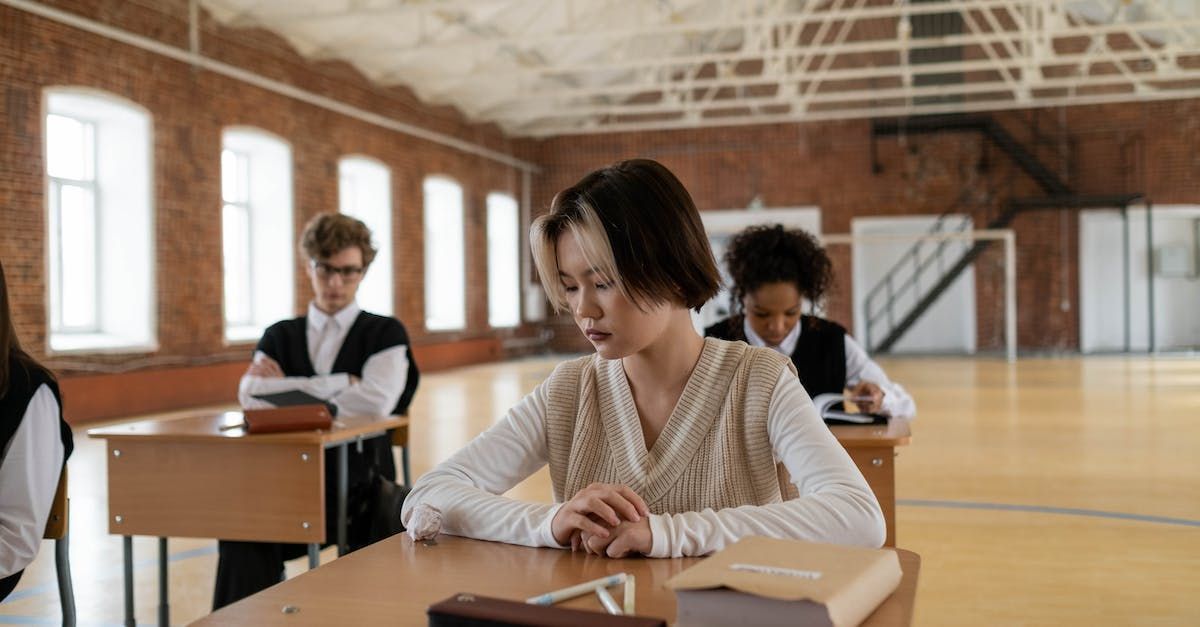
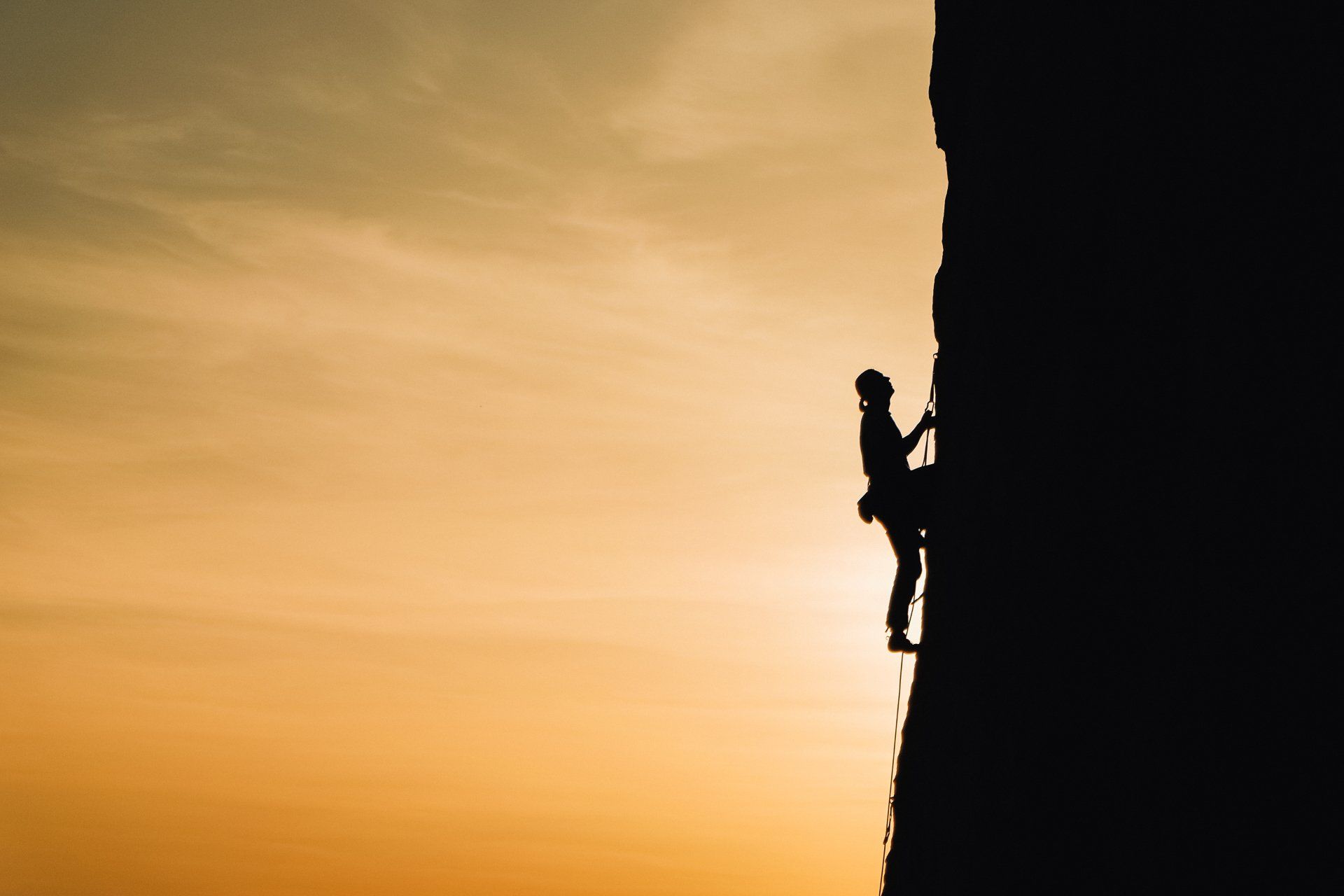
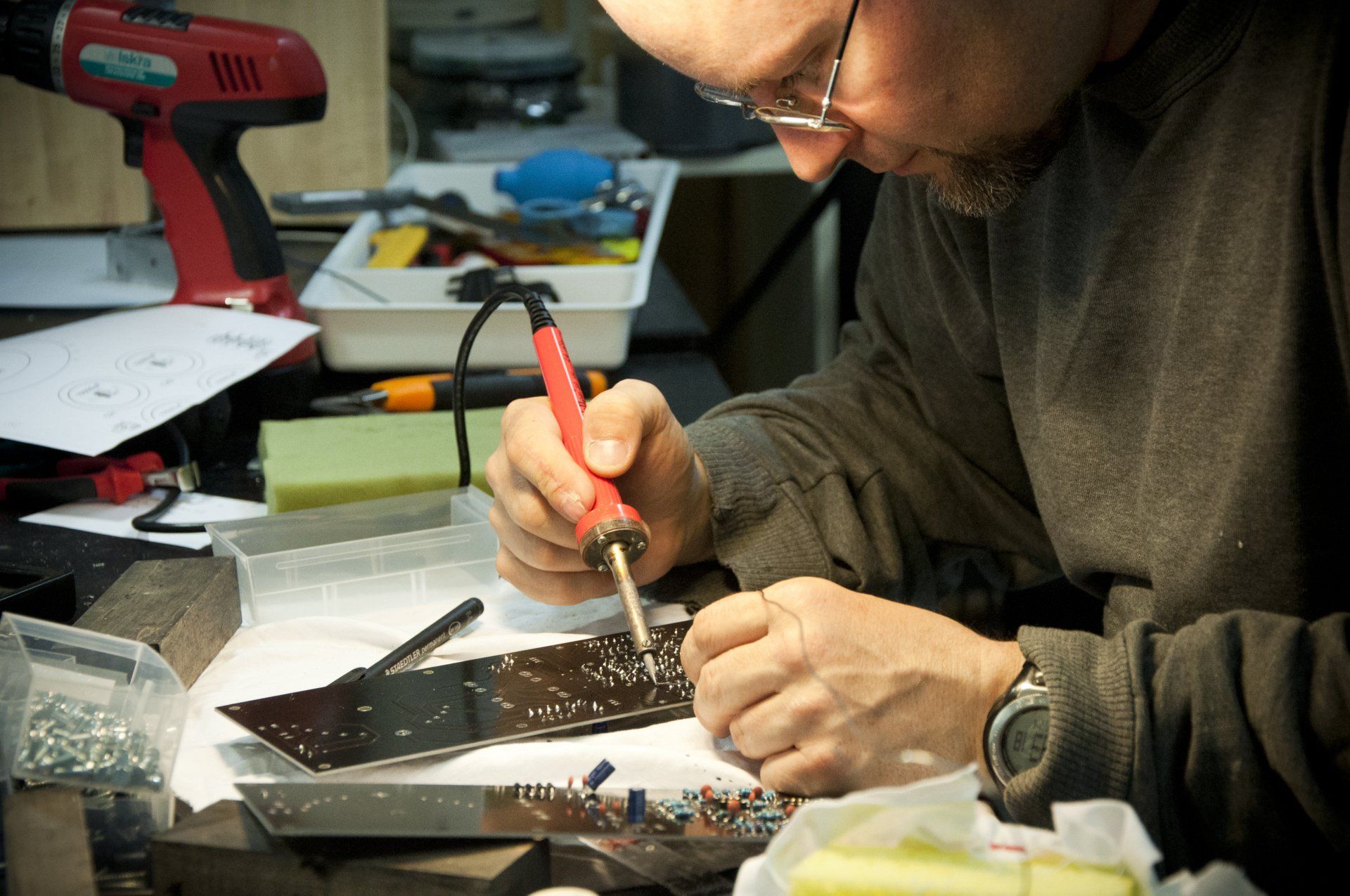
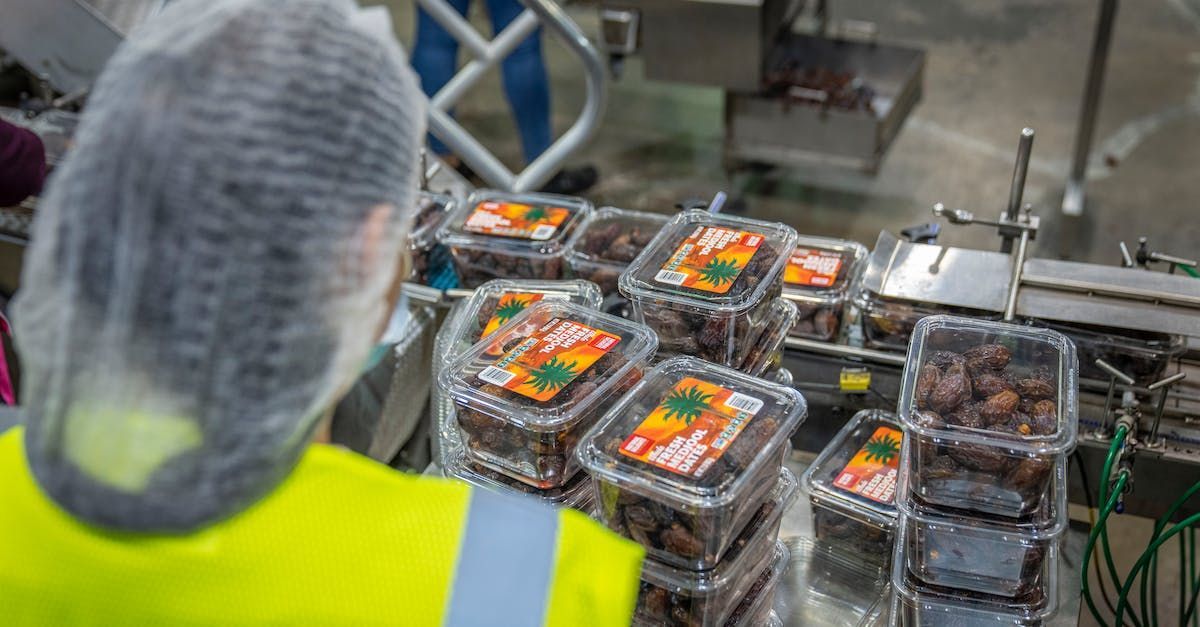
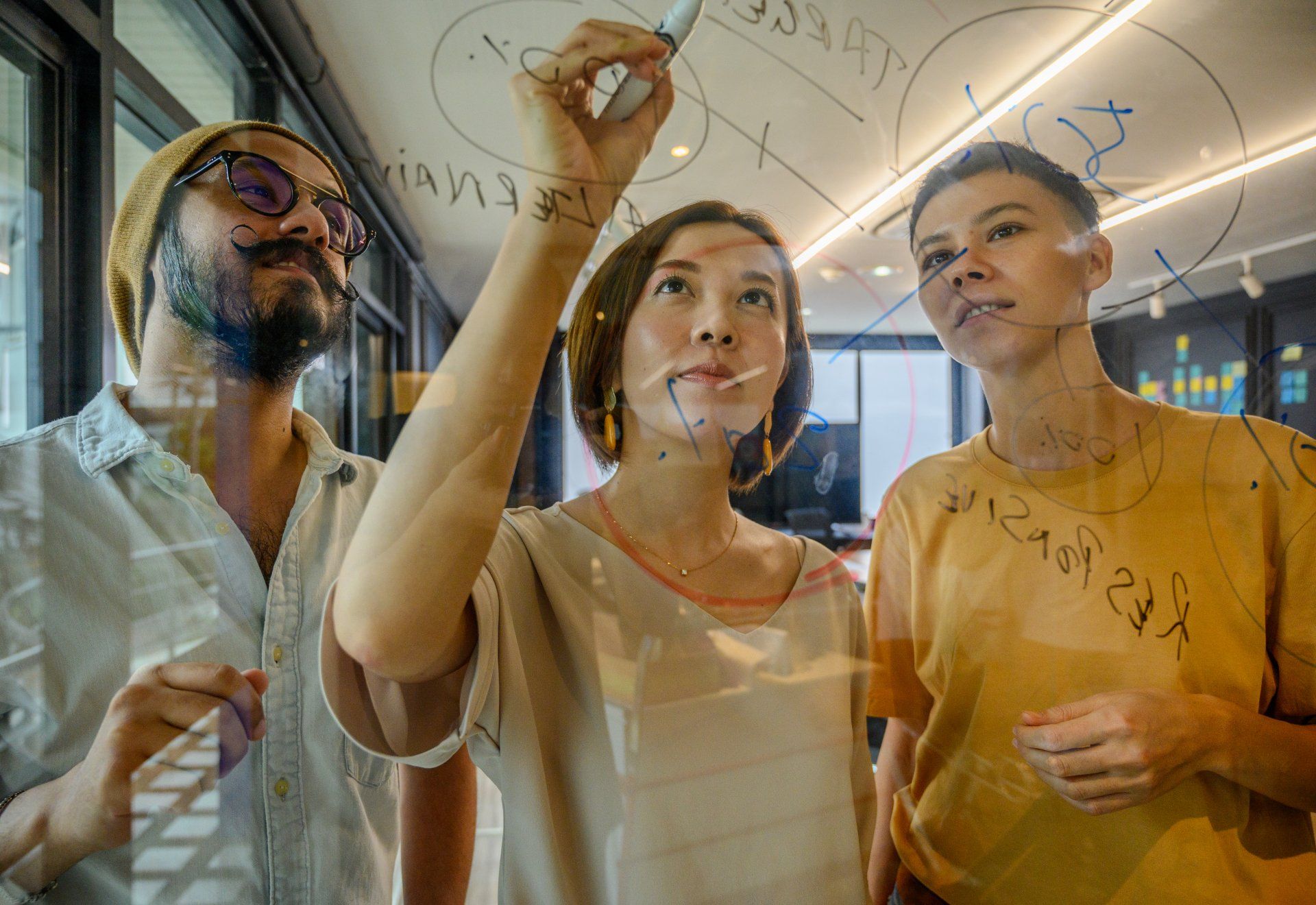
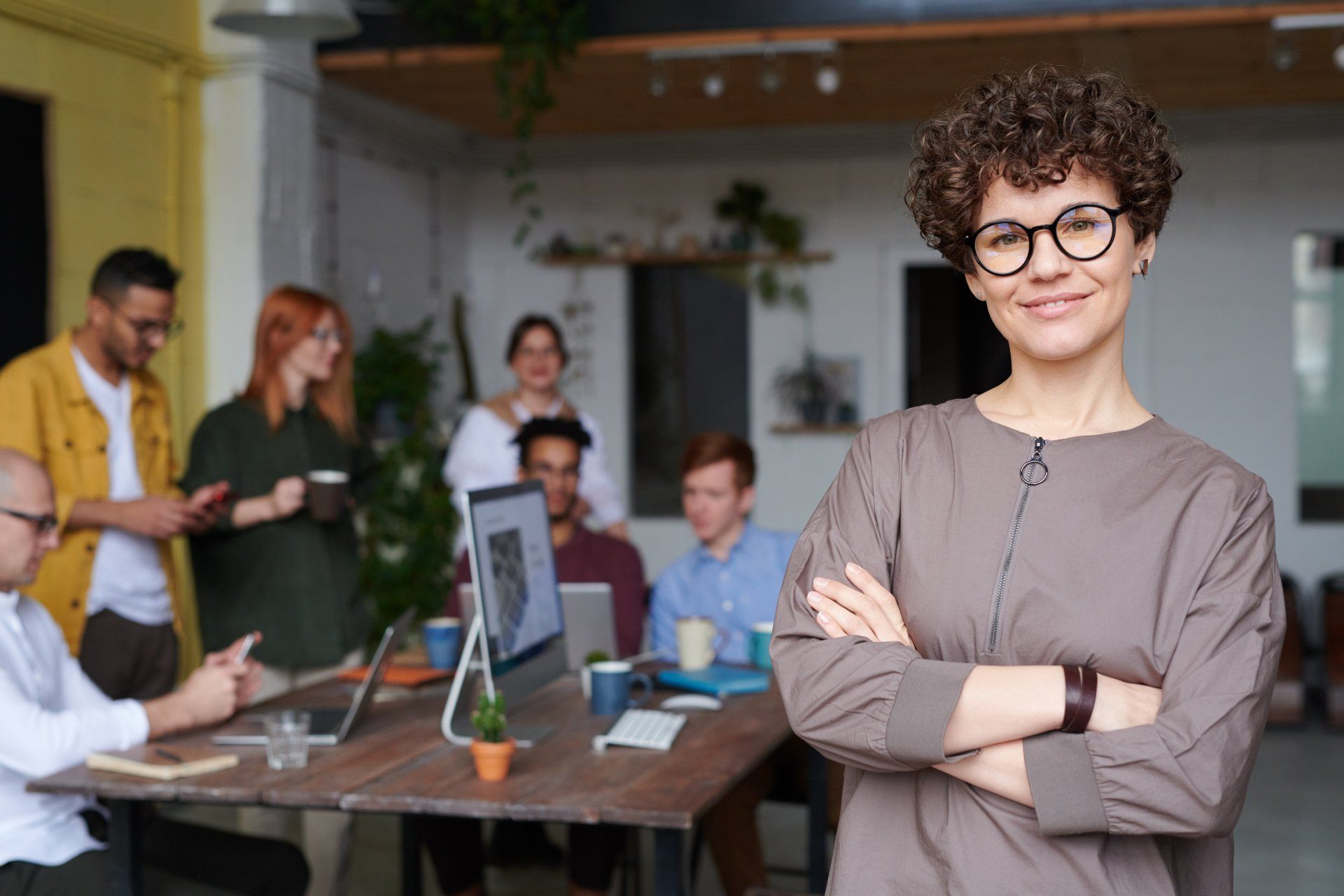
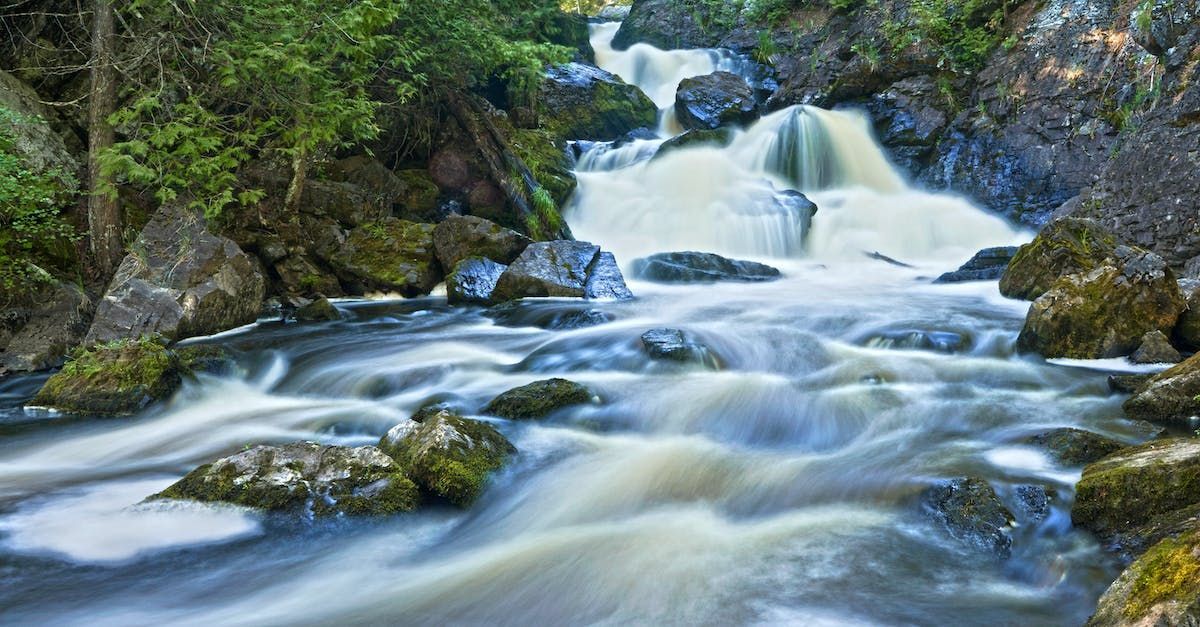
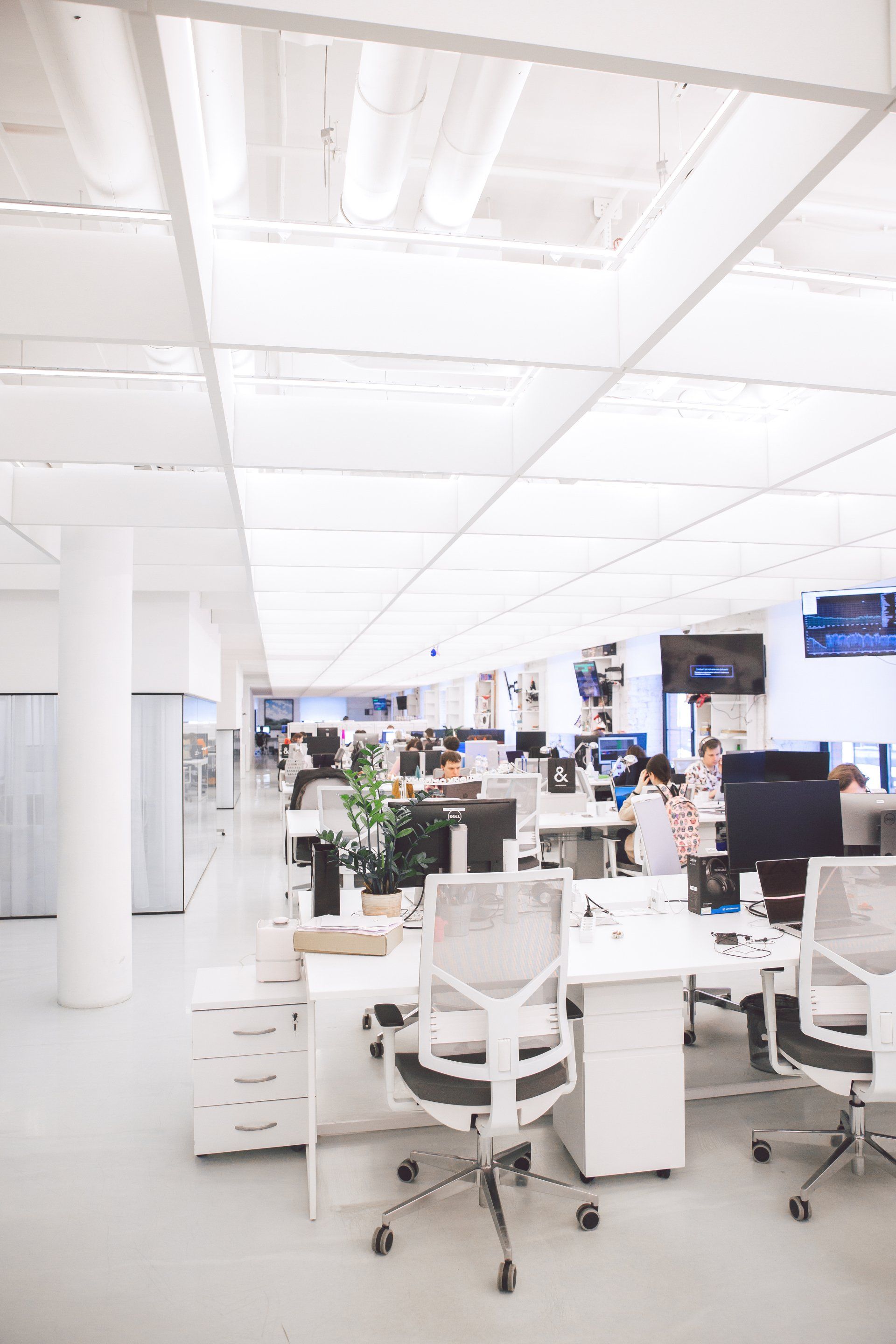